Aluminium: a lightweight, recyclable and metallic material
PDF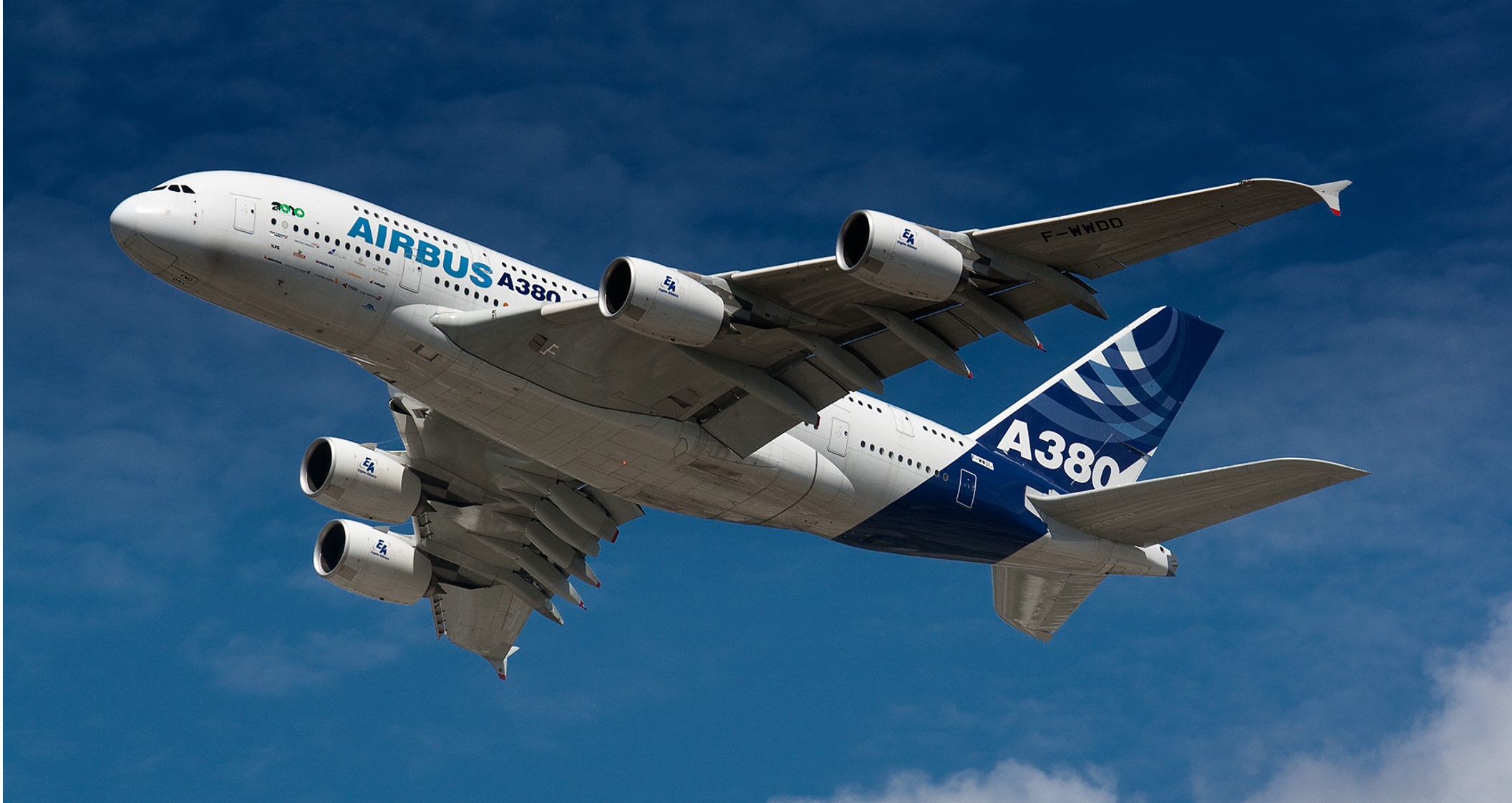
In today’s world, lightweight technology has become the key to the development of many industries as environmental awareness increases and energy efficiency is pursued. Aluminium, as a lightweight metal, is widely used in industries such as automotive, aerospace, and packaging due to its unique physical and chemical properties, such as low density, high strength, corrosion resistance, and recyclability. Research on lightweight aluminium materials not only helps improve energy efficiency and reduce fuel consumption, but also significantly reduces carbon dioxide emissions, which plays a positive role in environmental protection. In this article, we will delve into applications of aluminium and its alloys in lightweight technology, and the ways to push the frontier development of aluminium science and technology through innovative technology such as integrated die casting and the development of aluminium foam, to make the future greener and more sustainable.
1. Basic properties of aluminium
In the 130 years since its discovery, aluminium has gone through a transition from being a “precious metal” to overcapacity, and to now being in a great demand in the lightweight materials market (Table 1). Aluminium is the second most widely used metal, following iron (ferrous metal) because of its properties of being lightweight, corrosion resistant, ductile, rollable, and recyclable.
Table 1. Consumption structure of aluminium in downstream industries in China in 2022 (Source: USGS Data)
1.1 Light weight
The relative atomic mass of aluminium is quite small among metals. Compared to that of iron (55.85 g/mol) and copper (63.55 g/mol), aluminium is only 26.98 g/mol, and its density is merely 2.70 g/cm³, much lower than that of iron (7.87 g/cm³) and copper (8.92 g/cm³). These properties make aluminium an ideal lightweight material. In the industries such as aerospace, automotive, transportation and machinery manufacturing, the use of aluminium can significantly reduce the weight of structures, thereby enhancing energy efficiency and environmental performance. Because of its light weight, aluminium is widely used in materials for aircraft, earning its reputation of a “metal with flying wings.”
1.2 Corrosion resistance

The thickness of the passive film that forms naturally on aluminium is only 5~20 nm, which is far from sufficient for the widely-used aluminium alloys. Therefore, it’s necessary to artificially create an ideal protective oxide layer. The thickness of chemical oxide film is generally 1~3 µm, while the thickness of common anodized film can reach 3~30 µm. As a result, surface treatment technologies such as anodic oxidation (Figure 1) and microarc oxidation for aluminium have been developed.
1.3 Plasticity

1.4 Recyclability

2. Development of aluminium
2.1 Origin and history

2.2 Electrolysis theory

The chemical equations of the process are very complicated, but can be simplified as follows:

- Reaction at the cathode: 4 Al 3+ + 12 e– = 4 Al
- Reaction at the anode: 6 O 2- + 3 C – 12 e– = 3 CO2
- Overall reaction: 2 Al2O3 + 3 C = 4 Al + 3 CO2
The actual chemical process is more complex [3], and will not be elaborated here.
The appearance of the Hall-Héroult process in 1886 was a landmark in the development of aluminium (Figure 6) [4]. In 1888, Bayer process, a low-cost method of extracting high-purity alumina from bauxite, met the demand of low-cost and high-yield aluminium production, and aluminium achieved large-scale industrial production.
2.3 Evolution of electrolytic technology
The development of modern aluminium electrolytic technology has two main origins.
- Aluminium Company of America (Alcoa): A pioneer in the aluminium industry
Alcoa was founded in 1888 by Charles Hall. As one of the world’s largest aluminium producers, Alcoa has been at the forefront of the aluminium smelting technology and manufacturing sector. Since the 1940s, Alcoa has developed a variety of pre-baked aluminium reduction cell technologies, including P155 (170 kA), Alcoa-697 (230 kA), and Alcoa-817 (280 kA), each marked by higher current intensities and corresponding increases in production efficiency. By pursuing high current, Alcoa has been able to increase production, reduce the unit cost, and improve energy efficiency to enhance economic growth and meet the market demand. However, the increase of current will significantly enhance the electromagnetic force and thermal effect in the electrolyzer, leading to an increase in the amplitude and frequency of the fluctuation of the cryolite-aluminium interface, and complexity of the fluctuation pattern, thus affecting the stability and efficiency of the electrolysis process. Alcoa is a typical representative both in the world’s modern aluminium electrolytic technology and in the development of modern industry and science and technology. Similarly, its technical advancements have been significant in driving industrial progress.
- Pechiney (AP): A leader of modern aluminium electrolysis technology
Pechiney is the world’s preeminent representative of the aluminium industry, with international leadership in aluminium electrolysis technology. Pechiney uses its abundant hydroelectric resources in the south of France to obtain low-cost electricity and maximize the efficiency of aluminium electrolysis production through technological optimization and production improvements. From 1940 to 1978, the Saint-Jean-de-Maurlenne aluminium electrolysis plant underwent several modernization processes, leading to a continuous increase in the capacity of its electrolytic cells and driving technological advancement. It was here that the prototype for the AP series of aluminium electrolysis technologies was developed, making the plant a birthplace of modern aluminium electrolysis innovations.
However, the aluminium electrolysis process generates exhaust gases including fluoride, sulfur dioxide, fluorocarbons and dust, and these pollutants have a serious impact on the environment. In the 1970s, as the production scale of Pechiney Aluminium Plant continued to expand, pollution that it caused also became increasingly serious, especially the fluoride emission. Fluoride is a toxic substance that poses a serious hazard to the environment and human health. Due to the inadequate exhaust gas treatment system, a large amount of fluoride is emitted directly into the air, polluting the surrounding environment. As pollution intensified, local residents and environmental organizations began to protest, demanding that the company take measures to reduce pollution. Extensive media coverage also drew national attention.
Under the joint efforts of the government and enterprises, the exhaust gas treatment technology of electrolytic aluminium has been gradually improved. Today, more enterprises use dry purification to treat exhaust gases. Dry purification can deal with almost all exhaust gases, absorbing 99% of hydrogen fluoride, insoluble fluoride and dust, preventing a large amount of waste gas entering the living environment. The adsorbent of dry purification uses alumina, the raw material of aluminium electrolysis. After purification, the fluorine-carrying alumina can enter the electrolysis tank as raw material, which not only makes up for the loss of fluoride salts but provides the raw material for electrolysis. Dry purification greatly improves the environmental protection, and sustainable production of the electrolytic aluminium industry. Over the past 50 years, the achievements of Pechiney in improving the efficiency of reduction cell have positioned it as a world leader in the development of aluminium smelting technology [5].
- Rapid Development of Electrolytic Aluminium in China

To date, in the newly established production line of reduction cell by Weiqiao Pioneering Group in Shandong province, the current intensity has reached 600 kA (with a capacity of 100 wt/a). The 600 kA-aluminium reduction cell energy-saving and carbon-reducing technology represents a groundbreaking innovation in the global aluminium electrolysis research [6]. It excels in energy efficiency, carbon reduction, longevity and environmental protection, propelling advancements in the aluminium industry and bolstering the international competitiveness of core aluminium electrolysis technologies.
2.4 Alloy technology and innovation
- Duralumin
Back in 1906, German chemist Alfred Wilm discovered that by adding a small amount of copper to aluminium, the hardness of aluminium could be significantly increased. This finding led to the birth of tough aluminium, later known as duralumin, as it was first introduced into industrial production by the German company Dürener Metallwerke. Duralumin typically has a tensile strength ranging from 300 to 500 MPa, offering high rigidity and hardness. These features have led to its widespread application in fields such as aerospace and aviation.
The promotion of Duralumin has ushered in a new era of aluminium alloying, where other metal elements are added to pure aluminium through specific processing techniques to achieve diversified performance. The tensile strength of aluminium alloys can reach 200-600 MPa, offering not only good plasticity and corrosion resistance but also suitability for various industrial applications, making aluminium alloys the second-largest industrial metal after steel.
The strength and hardness of aluminium alloys are improved mainly due to the presence of different alloying elements such as copper, manganese, and magnesium, which enhance the aluminium matrix through solid solution strengthening. Other elements like titanium, vanadium, and boron enhance performance by refining grain size and increasing nucleation, while cadmium and scandium mainly improve performance through second phase strengthening. The diverse combinations and arrangements of these alloying elements result in a wide variety of applications and properties for aluminium alloys.
- High entropy alloys (HEAs)
In 1995, Jein-Wei Yeh, a professor at National Tsing Hua University in Taiwan, proposed a novel idea to design alloys – High Entropy Alloys (HEAs). These alloys typically comprise five or more elements in nearly equal proportions, each element’s concentration ranging from 5% to 35%, maintaining a largely atomic ratio. The defining characteristic of HEAs is their mixing entropy, which exceeds the entropy of melting. They usually form simple solid solutions, including face-centered cubic (FCC), body-centered cubic (BCC) and hexagonal close-packed (HCP) structures.
HEAs are the focus of significant attention, as they contain multiple elements of different sizes and chemical properties, leading to lattice distortion effect. This distortion affects not only atomic spacing and the stability of lattice structures, but also the motion of dislocations, thus improving the mechanical properties and thermostability of the alloys. Besides, the combination of multiple elements slows down the diffusivity of atoms, resulting in sluggish diffusion effect. This helps the alloys to maintain better stability at high temperatures, hindering atom migration and grain growth, thus improving their resistance to deformation and creep. The combination also brings about the so-called “cocktail” effect, where the alloy’s properties are influenced not only by individual elements but also by the collective action of many. This effect enables HEAs to exhibit diverse properties, achieving a balance and optimization of various performance aspects, thereby enhancing their overall performance.
Due to their unique lattice structures and properties, HEAs have emerged as one of the most promising research subjects in materials science in recent years. They offer high strength, hardness, wear resistance, oxidation resistance, and corrosion resistance, demonstrating broad application potential in many areas, such as tools, cutters, molds, golf club heads, turbine blades, and high-temperature furnace resistant materials.
3. The application of aluminium in critical industries
3.1 A change-maker in the automobile industry

The lightweighting of automobile is an effective approach to enhance vehicle braking, safety and acceleration. Aluminium alloy materials are widely used in the automotive body structure, significantly impacting weight reduction. In China, emerging domestic electric vehicle producers usually adopt lightweight aluminium alloys as the primary structural material and components to meet longer range requirements. Achieving lightweighting without compromising strength poses higher demands on the structural properties of aluminium alloys. This is typically achieved through optimizing structures and increasing material thickness. Using lightweight aluminium alloys is the optimal solution to address automotive lightweighting challenges. In the future, aluminium alloys are expected to see broader development in the automotive manufacturing industry.
3.2 Preferred materials for aerospace

In addition to the lightweighting requirements in the automotive industry, when we travel comfortably in planes soaring through the sky, we may also wonder: Why can such a seemingly thin fuselage safely carry so many passengers? Due to their moderate cost and excellent workability (including extrusion, rolling, bending, and additive manufacturing), aluminium alloys have become an excellent choice for aerospace materials (Figure 9), which accounts for up to 80% of aircraft materials, and are mainly used in the production of lightweight structures, upper and lower wing skins, and wing stringers. Besides, the most widely used aluminium alloys are Al-Cu alloys, Al-Zn-Mg-Cu alloys, and Al-Li alloys.
3.3 Leader in Packaging Material
In sweltering summer, various drinks in the store are favoured by most people, whose cans are made of aluminium alloys, as shown in the picture (Figure 10). The can factories have stringent requirements for aluminium can materials, demanding not only good inherent quality, uniform chemical composition, and low gas and inclusion content but also sheet materials with uniform thickness, good shape, and excellent surface integrity. At present, the most used cans are drawn and ironed (DI) cans, i.e. double-sided cans produced by a thinning and deep drawing process. To obtain high quality aluminium, each process of can making is strictly controlled, from casting to hot rolling, cold rolling, finishing and others. Through these processes, 3104 H19 aluminium alloy plate is produced, featuring good mechanical properties, deep drawing properties and surface integrity. The current trend for DI cans is towards thin-walled and lightweight designs, with the thickness of the aluminium alloy for can bodies decreasing from 0.35 mm to 0.27 mm and 0.25 mm. In the future, it is expected to be further reduced to approximately 0.20 mm.

4. The innovative application of aluminium
4.1 Efficient integrated “die casting” technology

“Die casting” technology represents a special casting method. With this technique, liquid and semi-liquid aluminium is filled into the die casting mold cavity under high speed and pressure conditions and allowing the metal liquid to solidify rapidly into a casting under certain pressure. Integrated die casting technology involves the redesign of multiple independent components, that would typically require assembly in industrial design. Using ultra-large die casting machines, these components are formed in a single casting, resulting in complete parts that fulfill their original functions. It is apparent that, compared to conventional die casting, integrated die casting emphasizes large-area integration and is fundamentally different from casting individual parts. Compared with the traditional processes of stamping, welding, painting, and assembly, integrated die casting is characterized by one-piece molding [7] (Figure 11).
Compared to split welded casting, this casting method reduces the number of parts that need to be assembled, thereby reducing production complexity and assembly costs, lowering the total weight of the vehicle, improving fuel efficiency and reducing emissions, and improving vehicle handling and stability for an enhanced driving experience.
4.2 The development and application of aluminium foam

The traditional aluminium materials we are familiar with are characterized by their dense structures, but aluminium foam has a completely different structure. Unlike traditional aluminium, it comprises pores and skeleton matrix (which physically support pores). The other parts are filled with pores, making the material porous like a sponge. We refer to this type of aluminium material with a large number of dense bubble cavities as aluminium foam. The most prominent feature of aluminium foam is its lightweight and low density, which can even float on water (as shown in Figure 12). The emergence of aluminium foam has broken the dense structure of traditional aluminium materials. It also has many advantages, such as high-temperature resistance, sound insulation and noise reduction, and good electromagnetic shielding performance. It has been applied in aerospace, construction, and automotive industries and is gradually becoming a focal point in the research of new materials for the modern era.
With the outstanding combination of mechanical, thermal, acoustic, energy absorption, damping and electromagnetic shielding properties, aluminium foam has become a remarkable example of integrated functional materials. It represents a significant breakthrough in traditional aluminium materials application and opens up new avenues for diverse engineering projects and scientific disciplines. Today, “aluminium foam” stands at the forefront of material science research and has become a popular topic in the field.
However, as both structural and functional material, aluminium foam still confronts several challenges in engineering technology applications. Firstly, it exhibits relatively lower specific strength and stiffness compared to solid metals, which has limited its widespread applications in engineering. Additionally, current research on aluminium foam mainly focuses on room temperature conditions, with further in-depth studies needed on its properties and performance under harsh environments such as high temperatures and high pressures. Moreover, the uniformity of pores in aluminium foam remains an issue to be addressed.
Aluminium foam, as a newly developed lightweight alloy, is not as widely used as traditional materials. However, it is foreseeable that in the 21st century, known as the “century of materials”, the mounting pressure on environmental protection and China’s shift towards high-quality development will vigorously promote the advancement of new materials including aluminium foam.
5. Messages to remember
- The Bayer method, the basic process of which has remained virtually unchanged since its invention in 1888, remains the primary method of producing aluminium oxide.
- The Hall-Héroult Process of producing aluminium by electrolysis, a principle first invented independently by Charles Martin Hall and Paul L.T. Héroult in 1886, remains the key method of global aluminium production today.
- Aluminium cans were initially produced by companies such as Coors Brewing and Royal Crown in 1960. The weight of two-piece aluminium cans have been reduced from the original 85 grams to approximately 15 grams today. They are lighter and easier to be recycled than three-piece steel cans. Through closed-loop recycling, a used aluminium can can enter the market in less than 60 days. The Mobius Loop, designed by Gary Anderson in 1970, reinforces the concept of waste reduction, reuse and recyclability.
- The “International Aluminium Institute: The Top 50 Moments in the History of the World Aluminium Industry” covers the key historical events in the development of the aluminium industry since the 19th century. These milestones collectively illustrate the important role of aluminium in modern industry and everyday life.
- Aluminium recycling consumes only 5% of the energy which is used to produce virgin aluminium and can reduce carbon dioxide and sulfur oxide emissions by more than 90%. Aluminium recycling can reduce production cost, protect the environment, and bring in great economic and social benefits.
Acknowledgements. This paper has been completed with great support from all parties. We would like to express our sincere thanks to all the people and organizations who have made efforts and contributions. Special thanks to Weiqiao Pioneering Group, special thanks to GAO Peng, ZHAN Aishuang, JIA Luanluan, ZHOU Weidong and others. and the University of Chinese Academy of Sciences, who provided valuable high-quality pictures and text materials, which greatly enhanced the richness and professionalism of the content. Thanks to the Lab of Electromagnetic Process of Materials (EPM) for providing technical support. Express additional thanks to the Binzhou Institute of Technology and the Metal Materials Center. I am also grateful to my master student FENG Qi for her hard work in collecting and editing this paper, and grateful to the professional translation team (SUN Libing, YANG Lingnan) from the Department of Foreign Languages of the University of Chinese Academy of Sciences for their quality translation work which ensured the accuracy and readability of the paper. Lastly, express gratitude to Academician LI Jiachun and Professor WANG Yanfen.
Notes and references
Cover image. The world’s largest passenger aircraft, the Airbus A380. [Source © Roger Green from BEDFORD, UK, CC BY 2.0, via Wikimedia Commons]
[1] Liu Peiying. Production and Application of Recycled Aluminum [M]. Chemical Industry Press, 2007.
[2] https://www.nps.gov/articles/000/wamocap.htm
[3] Einarsrud, K.E., Eick, I., Bai, W., Feng, Y., Hua, J., & Witt, P.J. (2017). Towards a coupled multi-scale, multi-physics simulation framework for aluminium electrolysis[J]. Applied Mathematical Modelling, 44, 3-24.
[4] Qiu Zhuxian. Prebaked Cell Aluminum Smelting [M]. 3rd Edition. Beijing: Metallurgical Industry Press, 2005.
[5] Liang Xuemin. Modern Aluminium Electrolysis Design and Intelligence [M]. Metallurgical Industry Press, 2020.
[6] Liu Jingqing. Iterative New Technology for Aluminium Electrolysis Successfully Developed at Weiqiao Pioneering Group. China Nonferrous Metals News, 2023-08-29. (chinania.org.cn)
[7] Wu, Yixuan, Wu Jixia. Performance de l’année dernière des sociétés cotées spécialisées dans l’intégration
The Encyclopedia of the Environment by the Association des Encyclopédies de l'Environnement et de l'Énergie (www.a3e.fr), contractually linked to the University of Grenoble Alpes and Grenoble INP, and sponsored by the French Academy of Sciences.
To cite this article: WANG Xiaodong (January 12, 2025), Aluminium: a lightweight, recyclable and metallic material, Encyclopedia of the Environment, Accessed April 24, 2025 [online ISSN 2555-0950] url : https://www.encyclopedie-environnement.org/en/physics/aluminium-a-lightweight-recyclable-and-metallic-material/.
The articles in the Encyclopedia of the Environment are made available under the terms of the Creative Commons BY-NC-SA license, which authorizes reproduction subject to: citing the source, not making commercial use of them, sharing identical initial conditions, reproducing at each reuse or distribution the mention of this Creative Commons BY-NC-SA license.