Copper, a sustainable material for the energetic transition
PDF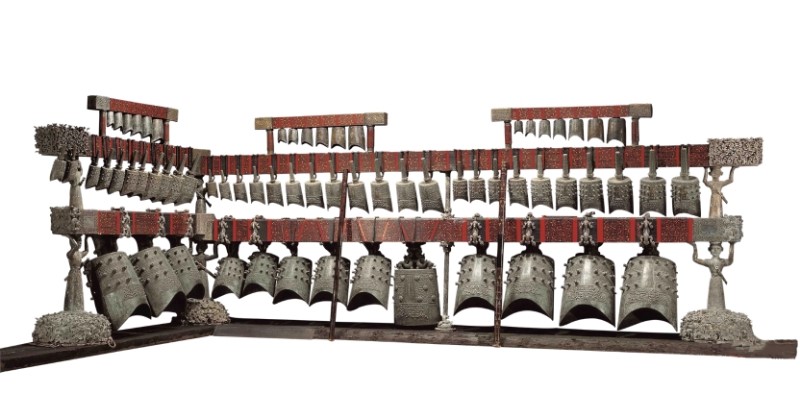
Copper, the first metal used by humanity, is at the heart of the current energetic transition. Thanks to its excellent thermal and electrical conductivity, it is indeed particularly valuable in the electrical and electronics industries, which account for more than half of its total consumption. Copper is indeed essential for manufacturing cables, wires, electric motors, transformers, switches, and circuit boards. Beyond these, it is integral to the production of industrial valves, fittings, instruments, plain bearings, molds, heat exchangers, and various pumps used in machinery and transportation. It ranks third in global production and usage among engineering metals, following iron and aluminum. The environmental impact of industrial materials must be evaluated from two key perspectives. First is the assessment of energy and resource consumption during the entire production process, from ore extraction to final product manufacturing. Second is the analysis of the product’s life cycle and reuse rate. Copper is recognised as a sustainable material. A testament to its durability is the Zenghouyi Chime Bells, depicted on the cover, a musical instrument comprising 65 bronze bells, remained intact after being buried underground for 2,430 years.
1. Copper and human civilisation
The discovery and use of new materials have always driven the progress of human civilization. Pottery, as the first man-made material, marked the end of the Stone Age, transitioning humanity to a more organized, though still primitive, era. During this period, mankind gradually developed new materials and invented a material with better performance and wider use than ceramic, the bronze. Bronze agricultural tools accelerated the development of agriculture, while bronze weapons ushered in the Cold Weapon era. The Bronze Age is recognized as the second period in the Three-Age System (Stone Age, Bronze Age, and Iron Age), a classification proposed by Danish archaeologist Christian Jürgensen Thomsen in 1836 [2].
In the ancient Near East, the Bronze Age (4,500BC–1,000 CE) began with the rise of Sumerian civilization and spanned the first 4,000 years of human history. This era was defined by the widespread use of bronze—an alloy of copper with tin, lead, antimony, or arsenic—for making tools and weapons. In China, the Bronze Age reached its peak during the Xia, Shang, and Zhou dynasties, continuing into the Spring and Autumn and Warring States periods. A notable example from this era is the Simuwu Rectangle Tripod, one of the largest extant bronze vessels in the world [2].
1.1 Basic properties of copper
Copper, with the chemical symbol Cu (from Latin Cuprum) and atomic number 29, is a transition metal found in the Earth’s crust and oceans. Copper constitutes approximately 0.01% of the Earth’s crust, though in concentrated deposits, its content can reach 3% to 5%. Most naturally occurring copper exists in the form of copper minerals or compounds. Copper physical properties are summarized in Table 1 [3]. It exhibits excellent electrical and thermal conductivity, along with low hardness and high plasticity, allowing it to be easily processed into products of various shapes for electrical and thermal applications.
Purple copper, also known as pure copper, has high electrical conductivity and plasticity but relatively low strength and hardness. When copper is alloyed with different elements, it forms various copper alloys with distinct properties. For example:
Cu-Ni (copper-nickel alloy), also known as white copper, where nickel is the primary alloying element.
Cu-Zn (copper-zinc alloy), commonly known as brass, where zinc is the primary alloying element.
All other copper alloys, including those with tin and other elements, are collectively referred to as bronze.
Table 1 Main Physical and Mechanical Properties of Copper [3].
1.2 Copper and cultural heritage
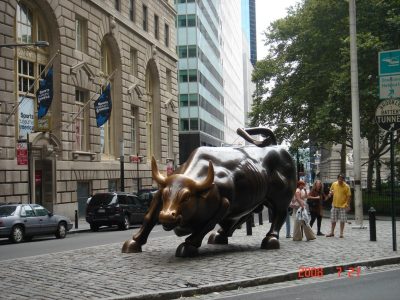
Figure 1 depicts the famous bronze bull statue on the Wall Street, designed by Italian artist Arturo Di Modica. Standing 3.4 meters tall, 4.8 meters long, and weighing 3.2 tonnes, the bull symbolizes “strength and courage,” representing the prosperity and wealth associated with Wall Street [4]. (similarly, the Chinese have long admired the bull’s vigor, reflected in the idiom “Niu Qi Chong Tian”, meaning “at the peak of one’s power” or “unstoppable energy.” This cultural parallel highlights the shared recognition of the bull’s enduring strength.)
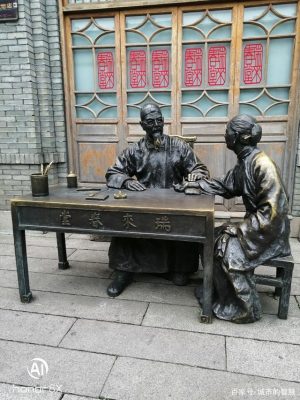
1.3 Copper role as currency
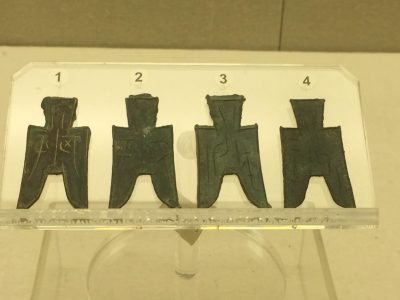
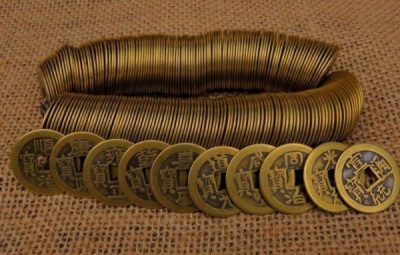
1.4 Copper in daily life and religion
Copper is a metal deeply intertwined with human life and culture. Since the Bronze Age over 2,000 years ago, people have used bronze to craft a variety of artifacts, including:

- Copper pot with engraved figures
- Copper seals
- Copper weapons
- Copper statues
- Copper washing utensils [5]
- Copper columns
- Copper lotus-shaped candle-stick holders
- Copper lion-shaped incense burners
- Copper armillary spheres

2. Smelting and processing of copper and copper alloys
2.1 Smelting
More than 200 copper-bearing minerals exist in nature, but only 20 are of industrial importance. These include primarily copper sulfide minerals and, to a lesser extent, copper oxide minerals, as outlined in Table 2 [6].
Table 2 Important copper minerals [6].
The development of copper smelting technology has evolved over centuries and can be classified into three major categories: pyrometallurgy, hydrometallurgy, and electrometallurgy. Currently, the extraction of copper from sulfide ores is predominantly carried out via pyrometallurgy, which accounts for approximately 85% of global copper production.
Pyrometallurgical processing involves increasing the copper content from its natural state of a few percent to around 20–30% through separation. Copper concentrates are then smelted in closed furnaces, such as blast furnaces, reverberatory furnaces, electric furnaces, or flash furnaces, to produce (also known as ice copper). This molten matte is transferred to a converter, where it is refined into crude copper. The crude copper undergoes further refining in another reverberatory furnace, occurs. It is then cast into anode plates for electrolysis, resulting in electrolytic copper with a purity of up to 99.9%. This process is efficient, with a copper recovery rate of up to 95%, and adaptable to various ore types. However, it is not environmentally friendly due to the emission of sulfur dioxide during the smelting and blowing stages. In recent years, processes such as the Baiyin process, Noranda process, and Japan’s Mitsubishi method have contributed to making pyrometallurgy more continuous and automated [6][7].
Modern hydrometallurgical (wet) copper smelting methods include sulfated roasting-leaching-electrowinning, leaching-extraction-electrowinning, and bacterial leaching. These methods are particularly suited for heap leaching, tank leaching, or in situ leaching of low-grade, complex ores, oxidized copper ores, and copper-containing waste. Wet smelting technology is gradually being adopted, and copper production using this method is expected to reach 20% of the total by the end of the century. One major advantage of wet smelting is its ability to significantly reduce the cost of copper extraction [6][7].
2.2 Refining
Common refining methods include zone refining, electrolytic refining, electron beam refining, and ion exchange. Among them, electrolytic refining is the most mature and widely adopted method.
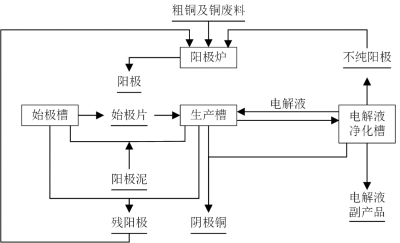
Oxidation reaction at the anode:
Here, M’ represents metals such as Ni, Pb, and As, which are more electronegative than copper. Due to their low concentrations, these metals dissolve preferentially into the electrolyte. Copper, being the primary component of the anode, undergoes oxidation to form Cu2+ ions. Oxidation reactions involving H2 O cannot occur at the anode due to the higher electrode potential compared to copper. Precious metals like Ag, Au, and Pt, with more positive electrode potentials, do not dissolve and instead settle as part of the anode sludge.
Reduction reaction at the cathode:
The standard electrode potential of hydrogen is more negative than that of copper. Additionally, the overvoltage at the copper cathode further lowers the electrode potential of hydrogen. As a result, under normal conditions, only copper deposits at the cathode, while hydrogen does not. Similarly, negatively charged metals with lower standard potentials than copper do not precipitate at the cathode [6].
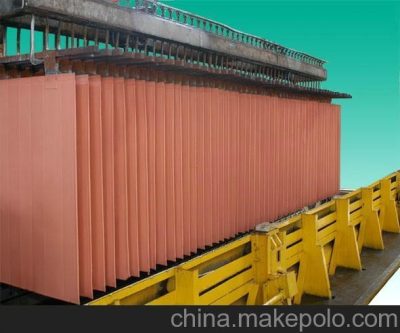
The electron beam refining (E-beam) method uses an electron beam to bombard raw copper under vacuum, generating high temperatures to melt the metal. In this process, impurities with low saturation vapor pressure are vaporized under vacuum. Directional solidification concentrates impurities with low solute distribution coefficients at the top, enabling further purification. While this method is more environmentally friendly than electrolytic refining, it is also more costly and less efficient.
2.3 Melting
Copper and copper alloys used in industry are primarily shaped into rods, wires, plates, foils, tubes, and other forms. To achieve these shapes, electrolytic copper plates must be melted at high temperatures. In some cases, alloying elements are added to produce copper alloy liquids, which are then cast into billets of various shapes.
The commonly used furnaces for melting copper and copper alloys are power-frequency core induction furnaces and medium-frequency induction furnaces. Power-frequency core induction furnaces are primarily used for large-scale continuous casting, while medium-frequency induction furnaces are suitable for producing multiple types of billets in small batches.
Copper alloy melting can cause significant environmental issues, particularly when the alloy contains low-melting-point or volatile elements. For example, brass, an alloy of copper and zinc (Cu-Zn), is highly valued for its excellent mechanical and wear-resistant properties and is used in precision instruments, ship components, gun cartridges, coins, and more. Brass typically contains 30%-40% zinc.
Since the melting point of copper is 1083°C and the boiling point of zinc is approximately 907°C, the melting temperature of brass exceeds zinc’s boiling point, producing a large volume of zinc vapor that contributes to serious environmental pollution. Therefore, factories must install appropriate environmental protection equipment, such as fume extraction systems, above the melting furnaces.
2.4 Casting
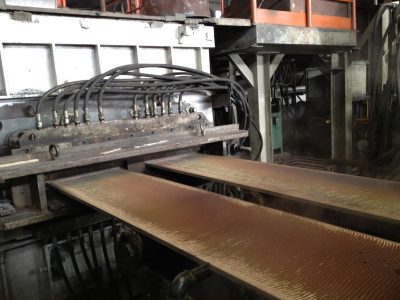
- Downward Vertical Semi-Continuous Casting
This method is used to produce round billets (ingots), square billets, thick slabs, and hollow round billets. It allows for a wide range of billet sizes and offers high productivity. However, the casting pit typically requires a depth of about 6 meters. Once the billet reaches a certain length, the process must be paused, and the billet removed. The crystallizer must also be cleaned before the next casting cycle. Both the top and bottom of the billet require trimming. - Horizontal Continuous Casting
This method is used for producing round billets, strips, and hollow round billets. It features continuous casting, where cutting saws trim the billets to the desired lengths. However, this method is unsuitable for casting billets with large cross-sections. - Upward Continuous Casting
This technique is used to produce round billets, strips, and hollow round billets. It allows for continuous casting, where billets can be directly rolled. However, it is also unsuitable for large cross-sections, and due to the anti-gravity nature of the process, the internal densification of the billets is slightly inferior.
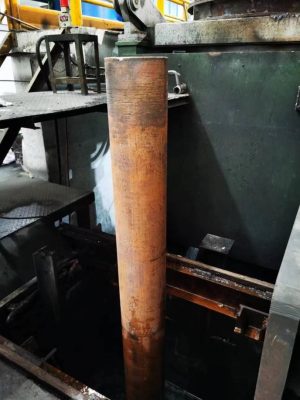
2.5 Forming
Copper has a face-centered cubic structure, allowing it to deform plastically with ease. This makes it possible to process copper and its alloys into various shapes such as plates, strips, foils, rods, wires, and tubes.
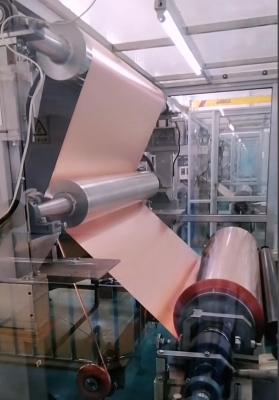
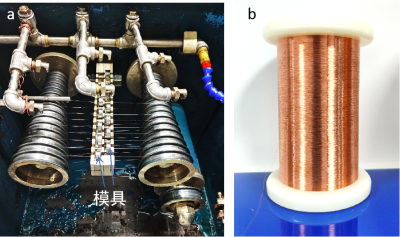
3. Applications of copper in key industries
3.1 Heat transfer
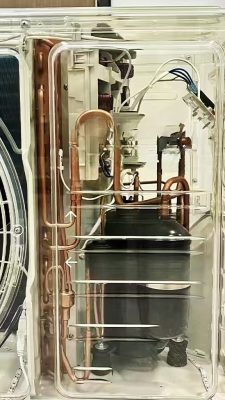

3.2 Electrical conductivity
Copper-silver alloy wires, with silver as the primary alloying element, possess exceptional electrical conductivity, mechanical strength, abrasion resistance, fusion-weld resistance, and thermal stability. Enameled wires made directly or coated with insulating layers (as shown in Figure 12) are extensively used in consumer electronics such as headphones, mobile phones, computer voice coils, and semiconductor bonding wires. In audio and video transmission, these wires provide high-fidelity signal transmission, exhibiting excellent resistance to high-frequency signal attenuation. This ensures clear audio and video transmission and meets the growing demand for high-speed data transfer. In bonding wire applications, copper-silver alloy wires offer a cost-effective alternative to gold wires, combining high electrical conductivity with superior mechanical strength. Their excellent ductility and resistance to breakage enable stable connections in high-speed bonding equipment, significantly reducing the risk of wire failure. These characteristics make copper-silver alloy wires an ideal material for high-performance electronics, balancing reliability and cost-effectiveness, and advancing the development of lightweight, high-performance electronic devices.
With the rapid development of integrated circuit technology, lead frames—critical components in integrated circuits—must continually improve in performance. As the chip carrier in integrated circuits, the lead frame facilitates electrical connections between the internal circuit leads of the chip and external leads using bonding materials like gold, aluminum, and copper wires. It acts as a bridge connecting internal circuits with external connections. Lead frames are essential in most semiconductor integrated circuits, serving as a vital material in the electronic information industry.


3.3 Corrosion and wear resistance function


4. Recycling and reuse of copper and copper alloys
The environmental protection and reuse of copper during smelting, processing, and usage can be divided into two key areas: the extraction of precious metals from anode sludge during smelting and electrolysis, and the recycling and reuse of scrap copper.
4.1 Recovery of precious metals from anode sludge [9]
Anode sludge from copper electrorefining accounts for approximately 1% of the total output and contains valuable precious metals such as gold, silver, platinum, and palladium, making it highly valuable for recycling. Efforts to recover these metals focus on minimizing secondary pollution and ensuring compliance with emission standards for the “three wastes” (waste gas, waste liquid, and solid waste). The goal is to foster circular use of copper resources while reducing pollution emissions, thus supporting the sustainable development of the copper industry.
The hydrometallurgical process for recovering precious metals like gold and silver involves the following steps:
- Precious metal enrichment: Impurities are removed to create optimal conditions for comprehensive recovery. Key pollutants include roasting dust from anode sludge, SO2 emissions, sulfuric acid mist, and arsenic-containing waste alkali generated during copper extraction.
- Gold extraction: Gold is leached from the solution and then reduced, with sulfuric acid mist and waste acid being the primary pollutants.
- Silver extraction: Silver is leached and recovered as silver powder. The main pollutant is the alkaline waste solution (pH ~13), which contains high concentrations of sodium sulfite.
4.2 Recycling and reuse of scrap copper
With the rapid development of the circular economy, recycled copper has become an essential resource. Two primary methods for producing recycled copper are:
- Direct utilization method: Scrap copper is directly melted to produce various grades of copper alloys or refined copper.
- Electrorefining method: Scrap copper is processed through pyrometallurgy into anode copper, which is then electrolytically refined into high-purity copper, with valuable elements recovered during the process.
Direct utilization of scrap copper can save over 80% of the energy compared to copper production through smelting ore and electrolytic refining, and around 50% compared to traditional electrolytic refining alone. However, the electrolytic process poses significant environmental risks. Therefore, properly sorted and separated scrap copper should be directly melted to minimize metal losses and reduce environmental pollution. The main recycling processes include:
- Sorting: this involves crushing, cleaning, and degreasing copper materials to separate non-metallic contaminants and non-copper metals like iron, aluminum, and stainless steel. This step ensures different grades of copper are categorized correctly for further processing.
- Separation: surface contaminants such as coatings, plating, and soldering materials are removed. Low melting-point brazing materials, plating metals, and paint films from waste electromagnetic wires are also recovered. This purification improves the quality and usability of recycled copper, while ensuring the safe disposal or repurposing of hazardous materials.
- Utilization: the sorted and purified copper is smelted in metallurgical or induction furnaces to produce high-quality oxygen-free copper rods or various copper alloys. These alloys are used to manufacture simple brass, complex lead-free brass, corrosion-resistant brass (aluminum and tin brass), tin phosphor bronze, white copper, and leaded brass, preserving quality and ensuring effective recycling.
According to the China Renewable Innovation Alliance, China produced approximately 3.3 million tonnes of recycled copper in 2019, 3.25 million tonnes in 2020, 3.65 million tonnes in 2021, 3.75 million tonnes in 2022, and 3.95 million tonnes in 2023. The recycled copper accounts for about a quarter of the total electrolytic copper production in China. Globally, tonnes annually in recent years, accounting for 30.7% of total electrolytic copper production, of which the United States is about 2 million tons per year, second only to China in recycled copper production.
This paper was made possible through the generous support of various individuals and organizations. I would like to extend my sincere gratitude to all those who contributed to this work. Special thanks go to Mr. Wang Yongru, Senior Engineer at Ningbo Jintian Copper (Group) Co., Ltd., for providing the pictures and content for Section 4.2, and to Prof. Tang Yuejin from Huazhong University of Science and Technology, Mr. Zhang Zhongtao, Senior Engineer at Golden Dragon Precision Copper Tube Group Co., Ltd., and Prof. Fu Ying from Zhongke Jingyi (Dongguan) Material Science and Technology Co. for supplying additional images. I am also grateful to Assoc. Prof. Zhang Yubo and Dr. Li Guoliang, at the School of Materials Science and Engineering, Dalian University of Technology, for contributing part of the text, and to Mr. Wang Yongru for his meticulous proofreading.
References and notes
Cover image. Zenghouyi Chime Bells of Hubei Provincial Museum [1]. [Source: Hubei Provincial Museum (hbww.org.cn)]
[1] The Zenghouyi chime bells were unearthed in 1978 from the tomb of Marquis Yi of Zeng in Suizhou, Hubei Province, dating back to the early Warring States period. The bell frame is 7.48 meters long and 2.65 meters high. The full set consists of 65 bells, arranged in three tiers and eight groups, suspended on an L-shaped bronze and wooden frame. The upper tier contains three groups of 19 niu bells, while the middle and lower tiers have five groups of 45 yong bells, and a special bo bell gifted to Marquis Yi by King Hui of the Chu State. The bells and the frame feature 3,755 inscribed characters, detailing numbering, historical records, musical notation, and theories of musical scales. Each bell can produce two distinct tones, with a complete chromatic scale in the central tonal range, allowing it to play music in five-tone, six-tone, or seven-tone scales.
[2] Zheng’an County Museum, China https://www.zabwg.cn/home/87/show.
[3] 360 Wenku.
[4] 360 Baike.
[5] Ancient Chinese often used bronze as a mirror, as referenced in New Book of Tang, authored by Ouyang Xiu and Song Qi:
“Using bronze as a mirror, one can correct one’s attire; using history as a mirror, one can understand the rise and fall of dynasties; using people as a mirror, one can discern personal gains and losses. I have always kept these three mirrors to prevent mistakes. Now that Wei Zheng has passed, I have lost one mirror.”
[6] Zhang, Y, Chen, X, Tian, B. et al. Copper and Copper Alloy Smelting, Processing and Application [M]. Beijing: chemical industry press, 2016.
[7] W. G, King. M, Schlesinger. M, Biswas. A. K, Extractive Metallurgy of Coppe [M], Beijing: Chemical Industry Press, 2006.
[8] Li, D., Research and Application of Casting Process for Large-sized Axial Tile Bushings, Annual Meeting of Foundry of Northeastern Three Provinces and Four Cities, Shenyang, 2017.
[9] Wang, F. and Wu, H. Comprehensive Utilisation and Management of Three Wastes in the Process of Scrap Copper Refining and Recycling of Precious Metals, Environmental Protection and Circular Economy [J], 2010, China Knowledge Network http://www.cnki.net.
The Encyclopedia of the Environment by the Association des Encyclopédies de l'Environnement et de l'Énergie (www.a3e.fr), contractually linked to the University of Grenoble Alpes and Grenoble INP, and sponsored by the French Academy of Sciences.
To cite this article: LI Tingju (February 22, 2025), Copper, a sustainable material for the energetic transition, Encyclopedia of the Environment, Accessed March 29, 2025 [online ISSN 2555-0950] url : https://www.encyclopedie-environnement.org/en/physics/copper-a-sustainable-material-for-the-energetic-transition-2/.
The articles in the Encyclopedia of the Environment are made available under the terms of the Creative Commons BY-NC-SA license, which authorizes reproduction subject to: citing the source, not making commercial use of them, sharing identical initial conditions, reproducing at each reuse or distribution the mention of this Creative Commons BY-NC-SA license.