L’aluminium : un matériau métallique léger et recyclable
PDF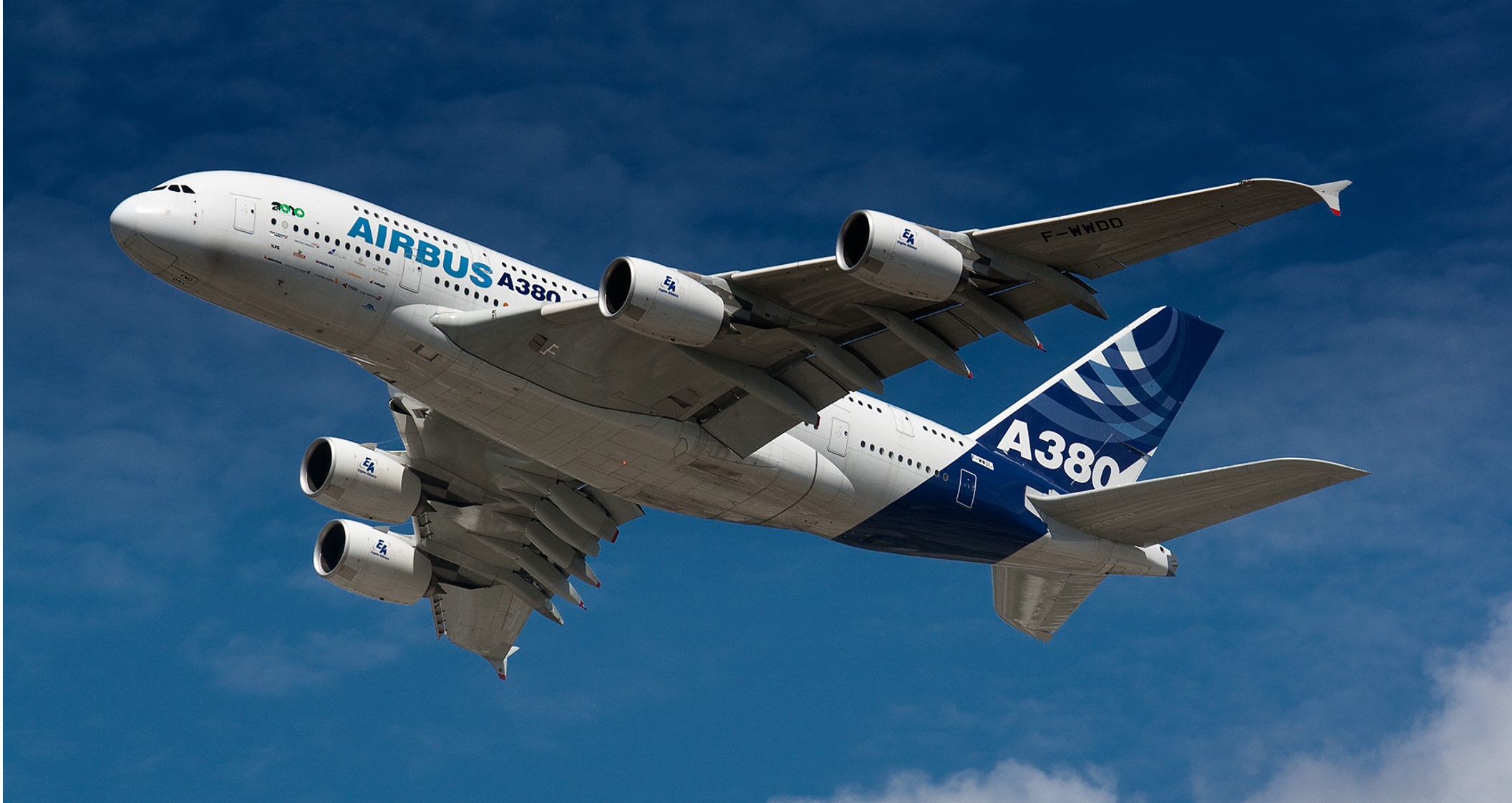
Dans le monde d’aujourd’hui, les technologies légères sont devenues les clés du développement de nombreuses industries dans un contexte d’une plus grande sensibilisation à l’environnement et de la recherche d’une plus grande efficacité énergétique. L’aluminium, en tant que métal léger, est largement utilisé dans des industries telles que l’automobile, l’aérospatial et l’emballage en raison de ses propriétés physiques et chimiques uniques, telles que la faible densité, la résistance à la corrosion et la recyclabilité. La recherche sur les matériaux légers en aluminium contribue non seulement à améliorer l’efficacité énergétique et à réduire la consommation de carburant, mais aussi à réduire considérablement les émissions de dioxyde de carbone, ce qui joue un rôle positif dans la protection de l’environnement. Dans cet article, nous nous penchons sur les applications de l’aluminium et de ses alliages, et sur les moyens de repousser les frontières du développement de la connaissance et de la technologie de l’aluminium grâce à des technologies innovantes telles que le moulage sous pression intégré et le développement de la mousse d’aluminium, en visant à rendre l’avenir plus vert et plus durable.
1. Propriétés de base de l’aluminium
Au cours des 130 années qui ont suivi sa découverte, l’aluminium est passé du statut de métal rare et précieux à un état de surcapacité, avant d’être aujourd’hui très demandé sur le marché des matériaux légers (Tableau 1). L’aluminium est le deuxième métal le plus utilisé, après le fer (métal ferreux), en raison de ses propriétés de légèreté, de résistance à la corrosion, de ductilité, de laminage et de recyclage.
Tableau 1. Structure de la consommation d’aluminium dans les industries en aval en Chine en 2022 (Source : données USGS)
1.1 Légèreté
La masse atomique de l’aluminium est relativement faible parmi celles des métaux. Par rapport à celles du fer (55,85 g/mol) et du cuivre (63,55 g/mol), celle de l’aluminium n’est que de 26,98 g/mol, et sa densité n’est que de 2,70 g/cm³, bien inférieure à celles du fer (7,87 g/cm³) et du cuivre (8,92 g/cm³). Cette légèreté fait de l’aluminium un matériau idéal. Dans des industries telles que l’aérospatial, l’automobile, le transport et la fabrication de machines, l’utilisation de l’aluminium peut réduire considérablement le poids des structures, améliorant ainsi l’efficacité énergétique et la performance environnementale. En raison de sa légèreté, l’aluminium est largement utilisé dans les matériaux des avions, ce qui lui a valu la réputation d’être un « métal à ailes volantes ».
1.2 Résistance à la corrosion
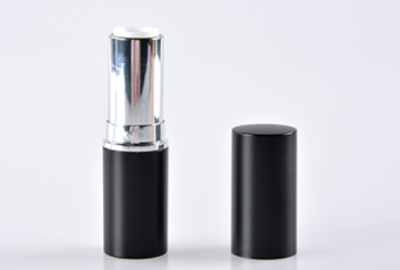
L’épaisseur du film qui se forme naturellement n’est que de 5 ~ 20 nm, ce qui est loin d’être suffisant pour les alliages d’aluminium largement utilisés. Il est donc nécessaire de créer artificiellement une bonne couche d’oxyde protectrice. L’épaisseur du film d’oxyde chimique est généralement de 1 ~ 3 μm, tandis que l’épaisseur du film anodisé commun peut atteindre 3 ~ 30 μm. Ce besoin de protection a amené à développer des technologies de traitement de surface telles que l’oxydation anodique (Figure 1) et l’oxydation par micro-arc.
1.3 Plasticité
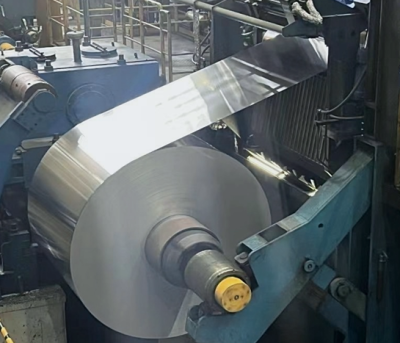
1.4 Recyclabilité
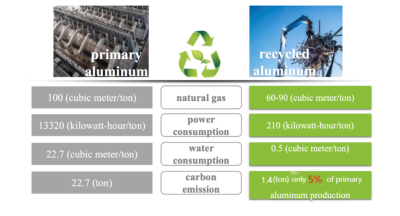
2. Développement de l’aluminium
2.1 Origine et histoire

En 1827, Friedrich Wohler a pu produire de l’aluminium par une réaction avec du potassium, mais la production d’aluminium par cette méthode était extrêmement faible, ce qui rendait l’aluminium rare et précieux. En 1884, pour protéger le Washington Monument contre la foudre, il a fallu en achever la construction en installant au sommet de la pierre de faîte une pyramide d’aluminium de 8,9 pouces de haut et de 100 onces (2,83495 kg). Ce capuchon en aluminium en forme de pyramide était la plus grande pièce d’aluminium au monde à cette époque (Figure 4, [2]). Par la suite, il a été découvert que la pointe sommitale du Washington Monument n’était pas constituée d’aluminium pur ; dans une lettre non datée, un scientifique anonyme a souligné que la composition de cette pyramide est de 97,75 % d’aluminium, 1,70 % de fer et 0,55 % de silicium [2].
2.2 Théorie de l’électrolyse
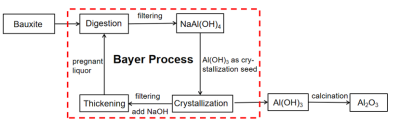
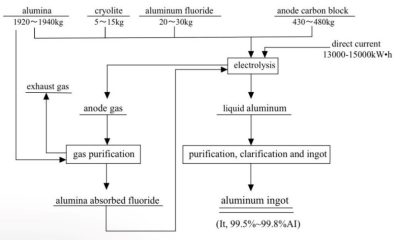
- Réaction à la cathode : Al 3+ + 3 e– = Al
- Réaction à l’anode : 2 O 2- = O2 + 4 e–
- Réaction générale : 2 Al2O3 = 4 Al + 3 O2
En 1888, le procédé Bayer, méthode peu coûteuse d’extraction d’alumine de haute pureté à partir de la bauxite, a pu répondre à la demande croissante de production d’aluminium à faible coût et à haut rendement, et la production industrielle d’aluminium a pu être réalisée à grande échelle. Mais l’apparition du procédé Hall-Héroult en 1886 marque un tournant dans le développement de l’aluminium (Figure 6) [3].
2.3 Évolution de la technologie électrochimique
Le développement de la technologie moderne de production de l’aluminium par électrolyse a deux origines principales.
- Aluminium Company of America (Alcoa) : un pionnier de l’industrie de l’aluminium
Alcoa a été fondée en 1888 par Charles Hall. Étant alors l’un des plus grands producteurs d’aluminium au monde, Alcoa a été à l’avant-garde des technologies de fabrication de l’aluminium par électrolyse. Depuis les années 1940, Alcoa a mis au point diverses technologies de cuves d’électrolyse précuites, notamment P155 (170 kA), Alcoa-697 (230 kA) et Alcoa-817 (280 kA), avec des intensités de courant de plus en plus élevées et des augmentations correspondantes du rendement de production (ou rendement de Faraday). Ces évolutions technologiques ont permis à Alcoa d’augmenter la production, de réduire le coût unitaire et d’améliorer aussi le rendement énergétique afin de renforcer la croissance économique et de répondre à la demande du marché. Toutefois, l’augmentation du courant électrique renforce considérablement la force électromagnétique et l’effet thermique dans la cuve d’électrolyse. Ceci entraîne une agitation de l’interface cryolithe-aluminium avec des fluctuations d’amplitudes et de fréquences variées qui affectent la stabilité et l’efficacité du processus. La compréhension et la modélisation de ces phénomènes ont constitué des défis particulièrement complexes. Alcoa est un représentant typique à la fois de la technologie moderne d’électrolyse de l’aluminium dans le monde et d’un développement industriel moderne appuyé sur des connaissances scientifiques et technologiques de plus en plus avancées.
- Aluminium Pechiney (AP) : Un chef de file de la technologie moderne d’électrolyse de l’aluminium
Aluminium Pechiney fut le premier représentant mondial de l’industrie de l’aluminium, avec un leadership international dans la technologie de l’électrolyse de l’aluminium. AP s’est appuyé sur les abondantes ressources hydroélectriques disponibles dans le sud de la France pour obtenir de l’électricité à faible coût et maximiser l’efficacité de la production d’aluminium électrochimique grâce à l’optimisation technologique et à l’amélioration des techniques de production. De 1940 à 1978, l’usine d’électrolyse de l’aluminium de Saint-Jean-de-Maurienne a fait l’objet de modernisations successives, ce qui a entraîné une augmentation continue de la capacité des cuves d’électrolyse et a permis leur évolution technologique. C’est là qu’ont été développées les cuves prototypes de la série AP, faisant de cette usine le berceau des innovations modernes en matière d’électrolyse de l’aluminium.
Cependant, le processus d’électrolyse de l’aluminium génère des émissions dans l’atmosphère de divers gaz, notamment du fluor, du dioxyde de soufre, des fluorocarbures et des poussières. Dans les années 1970, alors que la production des usines d’aluminium d’Aluminium Pechiney continuait à croître, la pollution engendrée devenait de plus en plus grave, en particulier les émissions de fluor, substance toxique qui constitue un grave danger pour l’environnement et la santé humaine. En raison de l’inadéquation du système de traitement de ces gaz, une grande quantité de fluor était émise directement dans l’atmosphère et polluait le milieu environnant. Face à cet accroissement de la pollution, les résidents locaux et des organisations environnementales ont commencé à protester et à demander que l’entreprise prenne des mesures pour réduire cette pollution. Une vaste couverture médiatique a également attiré l’attention au niveau national.
Grâce aux efforts conjoints du gouvernement et des entreprises, la technologie de traitement des gaz émis lors de la fabrication électrochimique de l’aluminium a pu être progressivement améliorée. Aujourd’hui, de plus en plus d’entreprises utilisent la purification à sec pour traiter ces émissions de gaz. Elle absorbant 99 % du fluorure d’hydrogène, du fluor et de la poussière insolubles, empêchant ainsi une grande quantité de polluants d’atteindre l’environnement. L’adsorbant utilisé pour la purification à sec est l’alumine, matière première de l’électrolyse de l’aluminium. Après la purification, l’alumine porteuse de fluor peut entrer dans le réservoir d’électrolyse en tant que matière première, ce qui non seulement compense la perte de sels de fluor, mais fournit également de la matière première pour l’électrolyse. Cette technologie de purification à sec améliore considérablement la protection de l’environnement et permet une production durable de l’industrie de l’aluminium d’origine électrochimique. Au cours des 50 dernières années, les réalisations d’AP en matière d’amélioration de l’efficacité des cuves d’électrolyse l’ont placée au premier rang mondial dans le développement de la technologie de production de l’aluminium par électrolyse [4].
- Développement rapide de l’aluminium électrochimique en Chine
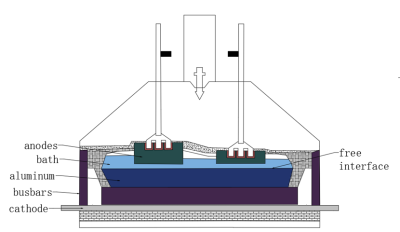
À ce jour, dans la nouvelle ligne de production de cuves d’électrolyse de Xinfa, filiale du groupe Weiqiao dans la province du Shandong, l’intensité du courant atteint 600 kA (avec une capacité de 100 t/a). Cette technologie d’économie d’énergie et de réduction des émissions de carbone de la cuve de 600 kA représente une innovation majeure dans la recherche mondiale sur l’électrolyse de l’aluminium [5]. Elle performe à la fois dans l’efficacité énergétique, la réduction des émissions de carbone, la longévité et la protection de l’environnement, propulsant les progrès de l’industrie de l’aluminium et renforçant la compétitivité internationale des technologies de base de production d’aluminium par électrolyse.
2.4 Technologie et innovation des alliages
- Duralumin
Déjà, en 1906, le chimiste allemand Alfred Wilm avait découvert qu’en ajoutant une petite quantité de cuivre à l’aluminium, la dureté de ce dernier pouvait être considérablement augmentée. Cette découverte a donné naissance à un alliage résistant, connu plus tard sous le nom de duralumin, qui a été introduit pour la première fois dans la production industrielle par la société allemande Dürener Metallwerke. Le duralumin a généralement une résistance à la traction comprise entre 300 et 500 MPa, ce qui lui confère une grande rigidité et une grande dureté. Ces caractéristiques lui ont valu d’être largement utilisé dans des domaines tels que l’aérospatial et l’aviation.
La promotion du Duralumin a ouvert une nouvelle ère des alliages d’aluminium, d’autres éléments métalliques pouvant être ajoutés à l’aluminium pur par le biais de techniques de traitement spécifiques afin d’obtenir des performances diversifiées. La résistance à la traction des alliages d’aluminium peut atteindre 200 à 600 MPa, offrant non seulement une bonne plasticité et une bonne résistance à la corrosion, mais convenant également à diverses applications industrielles. C’est ce qui fait des alliages d’aluminium le deuxième métal industriel après l’acier.
La résistance et la dureté des alliages d’aluminium sont améliorées principalement par la présence de différents éléments tels que le cuivre, le manganèse et le magnésium, qui renforcent la matrice d’aluminium par une mise en solution solide. D’autres éléments comme le titane, le vanadium et le bore améliorent aussi les performances en affinant la taille des grains et en augmentant la nucléation, tandis que le cadmium et le scandium permettent principalement de renforcer le durcissement. Les diverses combinaisons et dispositions de ces éléments d’alliage se traduisent par une grande variété d’applications et de propriétés pour les alliages d’aluminium.
- Alliages à haute entropie (HEA)
En 1995, Jein-Wei Yeh, professeur à l’Université nationale Tsing Hua de Taïwan, a proposé une idée novatrice pour concevoir de nouveaux alliages – les alliages à haute entropie (HEA). Ces alliages comprennent généralement cinq éléments ou plus dans des proportions presque égales, la concentration de chaque élément variant entre 5 % et 35 %. La caractéristique déterminante des HEA est leur entropie de mélange, qui dépasse l’entropie de fusion. Ils forment généralement des solutions solides simples, y compris des structures cubiques à face centrée (FCC), cubiques à corps centré (BCC) et hexagonales à emboîtement serré (HCP).
Les HEA font l’objet d’une attention particulière, car ils contiennent de multiples éléments de tailles et de propriétés chimiques différentes, ce qui entraîne un effet de distorsion du réseau. Cette distorsion affecte non seulement l’espacement des atomes et la stabilité des structures du réseau, mais aussi le mouvement des dislocations, améliorant ainsi les propriétés mécaniques et la stabilité thermique des alliages. En outre, la combinaison de plusieurs éléments ralentit la diffusivité aux échelles atomiques, ce qui a pour résultat une diminution forte des possibilités de diffusion. Ceci permet aux alliages de conserver une meilleure stabilité à haute température, en empêchant la migration des atomes et la croissance des grains, améliorant ainsi leur résistance à la déformation et au fluage. Cette combinaison de multiples éléments entraîne également l’effet dit « cocktail », où les propriétés de l’alliage sont influencées non seulement par des éléments individuels, mais aussi par l’action collective de plusieurs d’entre eux. Cet effet permet aux HEA de présenter des propriétés diverses, de parvenir à un équilibre et à une optimisation des différents aspects de la performance, améliorant ainsi leur performance globale.
En raison de leurs structures et propriétés uniques, les HEA sont devenus l’un des sujets de recherche les plus prometteurs dans le domaine de la science des matériaux au cours des dernières années. Ils permettent de prévoir une solidité, une dureté, une résistance à l’usure, une résistance à l’oxydation et une résistance à la corrosion élevées, démontrant un large potentiel d’application dans de nombreux domaines, tels que les outils, les fraises, les moules, les têtes de clubs de golf, les pales de turbines et les matériaux résistant aux fours à haute température.
3. L’application de l’aluminium dans les industries critiques
3.1 Un acteur du changement dans l’industrie automobile
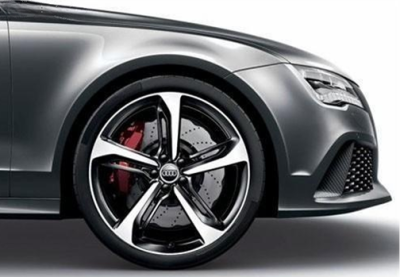
Les automobiles sont notre moyen de transport le plus courant. Les premières voitures n’étaient pas alimentées par de l’essence mais par de la vapeur, ce qui les rendait lourdes et gourmandes en énergie. Des recherches pertinentes ont montré que, quand le poids total en charge d’une voiture peut être réduit de 10 %, le rendement énergétique peut augmenter de 6 à 8 % ; en outre, une diminution du poids total en charge de 100 kg peut entraîner une réduction de la consommation de carburant aux 100 km de 0,3 à 0,6 L. De nos jours, la conservation de l’énergie et la réduction des émissions est un objectif mondial, mais les voitures sont également devenues un élément indispensable de notre vie. C’est pourquoi l’allègement des véhicules est devenu une tendance mondiale dans l’industrie automobile et constitue la priorité des constructeurs automobiles pour développer et produire les véhicules de la prochaine génération. Les alliages d’aluminium modernes, avec leur rapport poids/résistance supérieur, leur faible coût et leur grande résistance à l’usure, sont largement utilisés dans de nombreux composants structurels, ce qui les rend parfaitement adaptés à la tendance à l’allègement de l’automobile sur le marché actuel (Figure 8).
L’allègement des automobiles est une approche efficace pour améliorer le freinage, la sécurité et l’accélération des véhicules. Les alliages d’aluminium sont largement utilisés dans la structure de la carrosserie, ce qui a un impact significatif sur la réduction du poids. En Chine, les nouveaux producteurs nationaux de véhicules électriques adoptent généralement des alliages d’aluminium légers comme principaux matériaux structurels et composants pour répondre aux exigences d’une plus grande autonomie. Pour alléger les véhicules sans compromettre leur résistance, les propriétés structurelles des alliages d’aluminium doivent répondre à des exigences plus élevées. On y parvient généralement en optimisant les structures et en augmentant l’épaisseur des matériaux. L’utilisation d’alliages d’aluminium légers est la solution optimale pour relever les défis de l’allègement des automobiles. À l’avenir, les alliages d’aluminium devraient connaître un développement plus important dans l’industrie automobile.
3.2 Matériaux privilégiés pour l’aérospatial
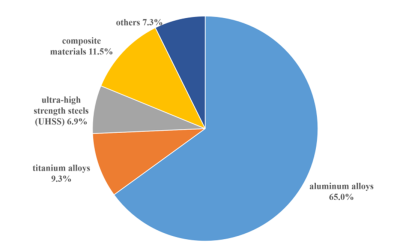
Outre les exigences de l’industrie automobile en matière d’allègement, lorsque nous voyageons confortablement dans des avions qui s’élèvent dans le ciel, nous pouvons également nous poser des questions : pourquoi un fuselage apparemment si fin peut-il transporter en toute sécurité autant de passagers ? En raison de leur coût modéré et de leur excellente usinabilité (extrusion, laminage, cintrage et fabrication additive), les alliages d’aluminium sont devenus un excellent choix pour les matériaux aérospatiaux (Figure 9), qui représentent jusqu’à 80 % des matériaux aéronautiques et sont principalement utilisés dans la production de structures légères, de peaux des ailes supérieures et inférieures et de longerons d’ailes. Les alliages d’aluminium les plus utilisés sont les alliages Al-Cu, les alliages Al-Zn-Mg-Cu et les alliages Al-Li.
3.2 Leader des matériaux d’emballage
Lors d’un été étouffant, de nombreux consommateurs préfèrent les diverses boissons disponibles dans des canettes en alliages d’aluminium (Figure 10). Les usines fabricant ces canettes doivent respecter des obligations strictes en ce qui concerne les matériaux utilisés, exigeant non seulement une bonne qualité intrinsèque, une composition chimique uniforme et une faible teneur en gaz et en inclusions, mais aussi des feuilles d’une épaisseur uniforme, d’une bonne forme et d’une excellente intégrité de surface. À l’heure actuelle, les canettes les plus utilisées sont étirés et repassés (DI), avec un matériau à double face produit par un processus d’amincissement et d’emboutissage. Pour obtenir un aluminium de haute qualité, chaque processus de fabrication de la canette est strictement contrôlé, du moulage au laminage à chaud, au laminage à froid, à la finition et autres. Ces processus permettent de produire des plaques d’alliage d’aluminium présentant de bonnes propriétés mécaniques, de bonnes propriétés d’emboutissage et une bonne intégrité de surface. La tendance actuelle pour les boîtes de conserve vise des conceptions à parois minces et légères, l’épaisseur de l’alliage d’aluminium pour les corps de boîte diminuant de 0,35 mm à 0,27 mm et 0,25 mm. À l’avenir, on s’attend à ce qu’elle soit encore réduite à environ 0,20 mm.
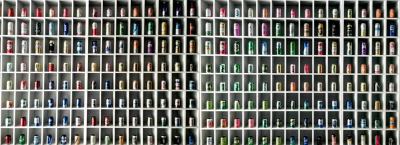
4. Des applications innovantes de l’aluminium
4.1 Une technologie efficace de moulage sous pression intégré
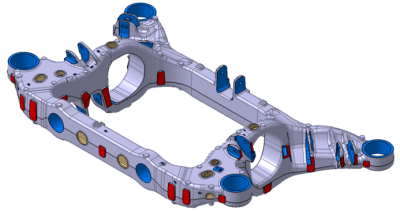
La technologie du « moulage sous pression » est une méthode spéciale : l’aluminium liquide ou semi-liquide est versé dans la cavité du moule de coulée sous pression et à grande vitesse, ce qui permet au métal liquide de se solidifier rapidement en une pièce moulée sous pression. Cette technologie implique la conception intégrée de plusieurs composants, qui nécessiteraient normalement un assemblage dans la conception industrielle. À l’aide de machines de moulage sous pression de très grande taille, ces composants sont formés en une seule coulée, ce qui permet d’obtenir des pièces complètes qui remplissent tout un ensemble de fonctions. Par rapport au moulage sous pression conventionnel, le moulage sous pression intégré s’appuie sur l’intégration de grandes portions du moule et est fondamentalement différent du moulage de pièces individuelles. Par rapport aux processus traditionnels d’estampage, de soudage, de peinture et d’assemblage, le moulage sous pression intégré se caractérise donc par la coulée d’une pièce unique [6] (Figure 11).
Par rapport au soudage de plusieurs pièces, cette méthode de moulage réduit le nombre de pièces à assembler, et donc la complexité de la production et les coûts d’assemblage. Elle diminue le poids total du véhicule, améliore son rendement énergétique, réduit les émissions et améliore la maniabilité et la stabilité du véhicule, permettant ainsi une conduite plus facile et plus agréable.
4.2 Développement et application de la mousse d’aluminium

Les matériaux traditionnels en aluminium que nous connaissons sont caractérisés par leur structure dense, mais la mousse d’aluminium a une structure complètement différente. Contrairement à l’aluminium traditionnel, elle comprend des pores et une matrice squelettique qui soutient physiquement les pores. Cet assemblage rend le matériau aussi poreux qu’une éponge. Ce type de matériau d’aluminium comportant un grand nombre de cavités, ou bulles, est appelé la mousse d’aluminium. Sa principale caractéristique est sa légèreté et sa faible densité, qui lui permet même de flotter sur l’eau comme le montre la figure 12. L’émergence de la mousse d’aluminium est une véritable rupture par rapport à la structure dense des matériaux traditionnels en aluminium. Elle présente également de nombreux avantages, tels que la résistance aux températures élevées, l’isolation acoustique et la réduction du bruit, ainsi que de bonnes performances en matière de blindage électromagnétique. Elle a déjà été appliquée dans l’aérospatial, la construction et l’industrie automobile et devient progressivement une direction majeure dans la recherche de nouveaux matériaux pour l’ère moderne.
Grâce à la combinaison exceptionnelle de propriétés mécaniques, thermiques, acoustiques, d’absorption d’énergie, d’amortissement et de blindage électromagnétique, la mousse d’aluminium est devenue un exemple remarquable de matériaux fonctionnels intégrés. Elle représente une avancée significative dans les applications traditionnelles des matériaux en aluminium et ouvre de nouvelles voies pour divers projets d’ingénierie et diverses disciplines scientifiques. Aujourd’hui, la mousse d’aluminium est à la pointe de la recherche en science des matériaux et a acquis une vraie popularité dans ce domaine.
Cependant, en tant que matériau à la fois structurel et fonctionnel, la mousse d’aluminium est encore confrontée à plusieurs défis dans les applications technologiques. Tout d’abord, elle présente une résistance et une rigidité spécifiques relativement plus faibles que celles des métaux solides, ce qui a limité ses applications dans le domaine de l’ingénierie. En outre, la recherche actuelle sur la mousse d’aluminium se concentre principalement sur les systèmes à température ambiante, de sorte que des études plus approfondies sont nécessaires sur ses propriétés et ses performances dans des environnements plus difficiles tels que les hautes températures et les hautes pressions. En outre, la réalisation d’une bonne uniformité des pores dans la mousse d’aluminium requière de nouveaux développements.
La mousse d’aluminium, alliage léger récemment mis au point, n’est pas aussi largement utilisée que les matériaux traditionnels. Toutefois, il est prévisible qu’au XXIe siècle, connu sous le nom de « siècle des matériaux », la pression croissante exercée sur la protection de l’environnement et l’évolution de la Chine vers un développement de haute qualité encourageront vigoureusement le développement de nouveaux matériaux, y compris la mousse d’aluminium.
5. Messages à retenir
- La méthode Bayer, dont le processus de base est resté pratiquement inchangé depuis son invention en 1888, reste la principale méthode de production d’oxyde d’aluminium.
- Le procédé Hall-Héroult de production d’aluminium par électrolyse, inventé indépendamment par Charles Martin Hall et Paul L.T. Héroult en 1886, reste aujourd’hui la principale méthode de production mondiale d’aluminium.
- Les canettes en aluminium ont d’abord été produites par des entreprises telles que Coors Brewing et Royal Crown en 1960. Le poids des canettes en aluminium en deux parties a été réduit de 85 grammes à l’origine à environ 15 grammes aujourd’hui. Elles sont plus légères et plus faciles à recycler que les canettes en acier à trois pièces. Grâce au recyclage en circuit fermé, une canette en aluminium usagée peut être mise sur le marché en moins de 60 jours. La boucle de Möbius, conçue par Gary Anderson en 1970, renforce le concept de réduction des déchets, de réutilisation et de recyclabilité.
- Le “International Aluminium Institute: The Top 50 Moments in the History of the World Aluminium Industry” couvre les événements historiques clés du développement de l’industrie de l’aluminium depuis le 19e siècle. Ces jalons illustrent collectivement le rôle important de l’aluminium dans l’industrie moderne et dans la vie courante.
- Le recyclage de l’aluminium ne consomme que 5 % de l’énergie utilisée pour produire de l’aluminium vierge et permet de réduire les émissions de dioxyde de carbone et d’oxyde de soufre de plus de 90 %. Ce recyclage réduit les coûts de production, protège l’environnement et apporte d’importants avantages économiques et sociaux.
Remerciements. Ce document a été rédigé avec l’appui de diverses parties. Je tiens à exprimer mes sincères remerciements à toutes les personnes et organisations qui ont déployé des efforts et apporté leur contribution. Un grand merci au groupe Weiqiao, un grand merci à Peng Gao, Aishuang Zhan, Luanluan Jia et à d’autres, ainsi qu’à l’Université de l’Académie des sciences chinoise, qui ont fourni des images et des textes de haute qualité, ce qui a considérablement amélioré la richesse et le professionnalisme du contenu. Merci au Laboratoire de Procédés Electromagnétiques des Matériaux (EPM) pour le soutien technique. J’adresse des remerciements supplémentaires à l’Institut de technologie de Binzhou et au Centre des matériaux métalliques. Je suis également reconnaissant envers mon étudiante en master Qi Feng pour son travail acharné dans la collecte et l’édition de cet article, et reconnaissant envers l’équipe de traduction professionnelle (Libing Sun, Lingnan Yang) du Département des langues étrangères de l’Université de l’Académie des sciences de Chine pour leur travail de traduction de qualité qui a assuré l’exactitude et la lisibilité du document. Enfin, j’exprime ma gratitude à l’académicien Li Jiacun et au professeur Wang Yanfen.
Notes and references
Cover image. Le plus grand avion de passagers au monde, l’Airbus A380. [Source © Roger Green from BEDFORD, UK, CC BY 2.0, via Wikimedia Commons]
[1] Liu Peiying. Production and Application of Recycled Aluminum [M]. Chemical Industry Press, 2007.
[2] https://www.nps.gov/articles/000/wamocap.htm
[3] Qiu Zhuxian. Prebaked Cell Aluminum Smelting [M]. 3rd Edition. Beijing: Metallurgical Industry Press, 2005.
[4] Liang Xuemin. Modern Aluminium Electrolysis Design and Intelligence [M]. Metallurgical Industry Press, 2020.
[5] Liu Jingqing. Iterative New Technology for Aluminium Electrolysis Successfully Developed at Weiqiao Pioneering Group. China Nonferrous Metals News, 2023-08-29. (chinania.org.cn)
[6] Wu, Yixuan & Wu Jixia. Performance de l’année dernière des sociétés cotées spécialisées dans l’intégration
L’Encyclopédie de l’environnement est publiée par l’Association des Encyclopédies de l’Environnement et de l’Énergie (www.a3e.fr), contractuellement liée à l’université Grenoble Alpes et à Grenoble INP, et parrainée par l’Académie des sciences.
Pour citer cet article : WANG Xiaodong (13 août 2024), L’aluminium : un matériau métallique léger et recyclable, Encyclopédie de l’Environnement. Consulté le 8 avril 2025 [en ligne ISSN 2555-0950] url : https://www.encyclopedie-environnement.org/physique/laluminium-un-materiau-metallique-leger-et-recyclable/.
Les articles de l’Encyclopédie de l'environnement sont mis à disposition selon les termes de la licence Creative Commons BY-NC-SA qui autorise la reproduction sous réserve de : citer la source, ne pas en faire une utilisation commerciale, partager des conditions initiales à l’identique, reproduire à chaque réutilisation ou distribution la mention de cette licence Creative Commons BY-NC-SA.