天然气和碳氢化合物的地下储存:能源转型的前景
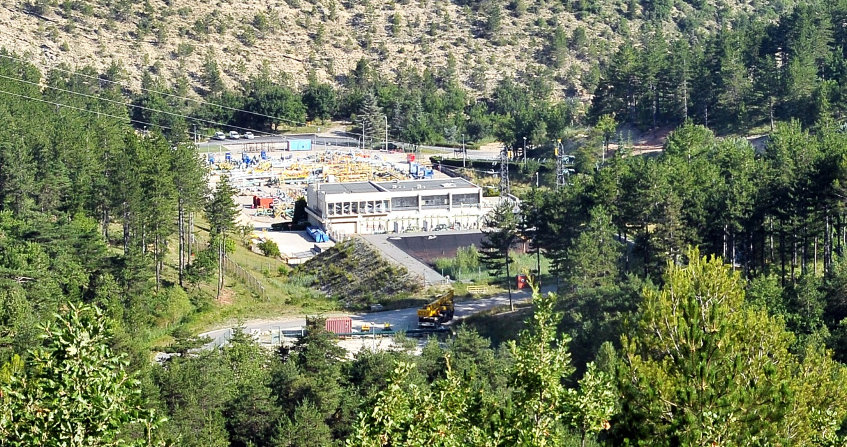
在穿过一队羊群和牧羊人之后,领略过马诺斯克镇(Manosque)旁吕贝隆(Luberon)地区壮丽风景的徒步爱好者可以沿着那些点缀在两山之间错落有致的办公室、泵站、井口(封面图片)等工业设备行进。徒步者并不会知道,在其脚下一公里的位置是法国战略石油储备的重要组成部分。此处储存着几乎可供法国使用两个月的近 1000 万吨石油,它们分布在大约 40 个数百米高的盐层洞穴中。接下来,我们将看到这项(石油)储存技术试图解决哪些问题,其成本、风险和机遇又是什么。
1. 为什么要储存碳氢化合物?
当前,碳氢化合物(石油和天然气)占法国能源消耗的一半以上,但几乎都来自进口。其中2015年,法国进口石油7700万吨,进口天然气 3440万吨 [1]。石油和天然气供应中断会导致灾难性的后果,例如 1973 年所谓的赎罪日战争之后的供应中断。因此,法国政府要求石油和天然气公司必须要有满足国家两到三个月需求的能源储备。就石油而言,法国绝大多数石油储存在马诺斯克(封面图片)。在天然气方面,除了战略考量之外,另一个需要关切的问题是由于供暖用天然气占天然气使用总量的三分之一,所以法国夏冬两季天然气的需求差异很大。
油气田等生产系统和管道、LNG 罐车等输送系统的建设都需要巨量的投资。为即刻满足一年当中最冷几天的需求高峰而加大投资在经济学上是荒谬的行为,因为这部分投资在一年中的其余时间里毫无用处。相比投资生产系统和运输系统,在自己国土上(或者在国土下)建立易于调动的(能源)储存库,可能会更好地“抚平”需求高峰。拿天然气存储来说,大多采用地下储备。所有的工业国家都有这样的地下储备。比如,美国在德克萨斯州和路易斯安那州的盐穴中建立了7 亿桶(1 亿吨)原油的“战略石油储备”,经美国总统签署命令后即可动用。
上述储存技术不会因能源转型而过时。风力发电或光伏发电具有间歇性,这就要求强大的储能能力。这种储能要求很有机会在地下得到满足。而这些设想中的储能技术最常受到的启发则来自现有的碳氢化合物储存技术。
2. 碳氢化合物储存技术
2.1. 含水层储能
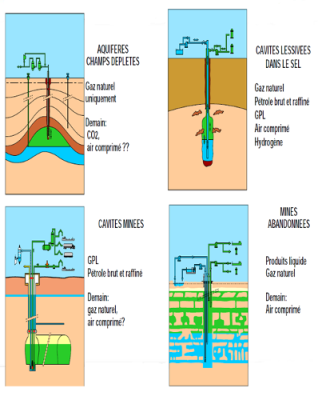
[图片来源:摄影地质库](图1 AQUIFERES CHAMPS DEPLETES含水层排空,Gaz naturel uniquement仅限于天然气,Demain次要的,CO2二氧化碳,air comprimé压缩空气;CAVITÉS LESSIVÉES DANS LE SEL盐浸空腔,Gaz naturel天然气,Pétrole brut et raffiné原油和精炼石油,GPL液化石油气,Hydrogene氢气;CAVITES MINEES洞式矿井;MINES ABANDONNEES废弃矿井,Produits liquide液体产品)
法国于 1958 年在位于伊夫林省贝恩斯(Beynes)的沃尔丁(Wealdien)推覆体首次应用了含水层储能技术。这种储能技术被专门用于储存天然气。其原理主要是通过开采井(图 2,区域 4)将气体注入,将原本存在于该层岩石孔隙中的水挤压出去,从而实现气体的存储。含水层(图 2,区域 2)必须符合以下特征:
- 足够的厚度(至少几十米)。
- 平均孔隙度φ(气体可在岩石中占据的空隙的体积比例)和平均渗透率K(它决定流体流动的难易程度)高。理想情况应满足φ= 20%、K = 10-12 m2是理想的情况。
- 盖层(图2,区域1)厚度充足,渗透率极低,气体进入其底部孔隙所需压力(即克服盖层材料孔隙中水的毛细管作用力,使气体进入这些孔隙的压力)高。要让比水还轻的天然气“泡泡”无处可逃,盖层下部必须是弧形的,同时一定不能有让气体溢出的裂缝。
- 盖层下方要有足够大的横向面积,它决定了储气库的大小(S = 5 km2可以满足要求)。

[图片来源:斯托伦吉](图 2 Coupe d’un stockage en aquifère 含水层储气库断面,Couverture étanche 防水罩,Reservoir 气藏,Station centrale 中心站,Puits d’exploitation: injection, soutirage 作业井:注入、采出,Puits de contrôle périphérique 外围控制井,Puits de contrôle de l’aquifère superieur 上层含水层控制井,aquifère superieur 上层含水层)
上述特征常见于优质采气用天然气藏。所以含水层储气库应同样天然满足这些特征,使存储的天然气稳定保存百万年之久。在美国,天然气通常储存于运营过的、所谓“枯竭的”天然气田或油田,而在法国的 13 个储气库中仅有一个采用这种储气方式。
注气驱水时,注气的压力要高于周边水回流到储气库(图 2,区域 2)的压力,但要低于气体进入盖层(图 2,区域 1)的压力。储气库顶部的最大压力梯度等于最大气压与储气层深度的比值,各储气点该值是固定的,均不能超过 0.015MPa/m(自然状态下,储气层内水的压力梯度约为 0.01 MPa/m)。假定储气库的高度为 20 m,则底部气体占据的体积为 V = Shφ = 5 km2 x 20 m x 20% = 2000 万 m3。如果这种气体在深度 H = 500 m 并且储气库顶部的压力梯度 γ = 0.012 MPa/m,则气体压力 γH = 6 MPa(60 bar)。因此,天然气存储在地下所占的体积比在大气压力下(PV = rT)小 60 倍,相当于地面上储存了 2000 万 m3 x 60 = 12 亿 m3,根据定义,它的质量是 12 亿 Nm3(Nm3 或标准立方米,是在常温常压下 1 m3 天然气的质量,1 Nm3 = 0.68 kg)。法国每年的天然气消耗量为 350 亿Nm3,而 13 个地下含水层储气库或枯竭油气藏储气库可储存 110 亿 Nm3 天然气。
储气是逐步实施的:第一年夏季往储气库储气,同年冬季抽取一部分使用,次年夏季往储气库存储更多天然气,直到大约20年后储气库达到最大储存量。在这一过程中,天然气储存库的范围逐步扩展,需要根据情况挖掘新的注采井(图 2,第 4 区),而一个储气库大约需要配置数十口注采井才能保证注采工作的顺利开展。储气库储存的天然气大约有50%会渗入到非常细小的孔隙中,无法再从中取出(“垫层气体”)。这部分天然气就成了储存损失,但这种损失只会发生一次。随着时间的推移,垫层气体占存储气体总量的比例越来越小
储存的气体必须保持封闭状态。经过初步识别,我们有可能探明储气库周围有利的几何和水文地质位置。再经逐步挖掘监测井,通过取样和测量(将缆绳投入井下,在缆绳的末端放置一个传感器,用于测定气体和水的含量、孔隙度、温度等),便可以对上述条件进行确认。在储气库的外围打一些钻孔(图 2,区域 5)监测水压。我们试图检测的并不是钻孔中是否有气体进入(与待监测区域的大小相比,钻孔数量较少,),而是监测各钻孔采集到的压力数据是否一致。为此,从一开始就要建立该储气库的水文地质模型,通过记录注入和抽取天然气的历史数据,加上连续监测的钻孔压力数据,就可以通过比较预测和测量数据(历史匹配),不断改进该储气库的水文地质模型。
监测系统通常包括一口抵达储气层上方含水层的探井(图 2,区域 6),该含水层具有足够渗透性(图 2,区域 7)。与外围探井相同,监测这口探井的水压,就可以判断储存的天然气是否泄漏。泄漏的天然气会积聚这个上方含水层里,该含水层也称为“控制”含水层。
储气用地下水水质的维护是储气库建设的一个关键问题,需要对注入的气体进行净化,并仔细监测重金属或苯。注入的天然气会增加地下水位的压力并可以改变其流体动力学。建设时需要各方签署协议,参与地下水保护和开发的所有各方共享收集到的信息,以确保对地下水进行最佳管理。
2.2. 无涂层的地下廊道储存
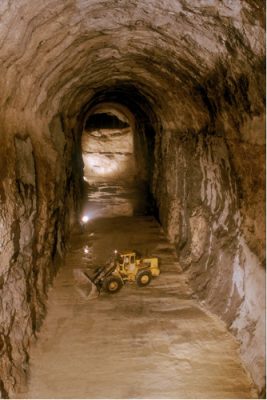
[图片来源:摄影地质库]
第二种技术是挖掘地下坑道(或地下坑道网络)。废弃的地下旧坑道也可以使用,例如在诺曼底的奥尔恩河畔迈(May-sur-Orne),就在一个废弃的铁矿采坑中储存了 500 万 m3 燃油。地下廊道每立方米的储藏成本很高(见下一节),但优点在于适用于多种地质条件(白垩、石灰石、片麻岩、花岗岩),因而被广泛应用于地质条件不允许其他任何类型储藏的国家(斯堪的纳维亚、日本)。大型地下坑道的容积可超过 100 万 m3。法国具有地质多样性的优势,在炼油厂地下或石油港口附近等有特定存储需求的地点,保留了一些储存量在 10 万 m3 级别的地下坑道。
坑道通过竖井与地面相连,竖井充满水,底部用厚混凝土塞封闭,通过该塞控制油气的充填和抽取。图 4 展示了在拉韦拉( Lavéra ,博什度罗纳, Bouches-du-Rhône )白垩地层挖掘的 18 米高的坑道。由于该地块是渗透性的, 要在坑道中保存油气,就需要使油气的压力低于坑道底部的水压,使水不断从围岩渗入坑道,以防止油气渗入围岩而泄漏,这就是所谓的“动态”密封。由于水进入坑道,就减少了可用于油气储存的体积,还有可能使油气的压力不断增加,以至于使油气渗入围岩。因此,必须连续通过抽注调节油气的压力。
在法国,碳氢化合物(丙烷或丁烷)以双相状态(液气平衡)储存,就像在打火机中一样,这进一步保证了安全性:坑道中可用体积的减少使气相凝聚成液体,而不会使压力持续增大。处于双相状态的丙烷,在 15°C 下的压力为 0.8 MPa,即 80 米水柱的压力:矿井水流量随地下水位下结构的深度而增加,因此坑道必须位于更深的地方,通常为 130 m,以便在限制矿井水流的同时保留足够的裕度。
以上液压状态必须始终保持稳定。例如,如果坑道顶部有土石坍塌的话,将导致坑道的最高点升高,同时防止气体反向渗入围岩的安全裕度将会减小。因此,在正式充填储存区域之前,必须仔细开展岩土工程研究,尽可能的加固风险点。原则上所储产品的压力可通过储存设施建设保持恒定,但必须注意防止储存的液体中挥发性组分(乙烷、甲烷),它们会在坑道顶部积累,逐渐改变该区域压力。
同样,区域上限的状态(浮油自由表面的深度)必须保持稳定,因此必须考虑到可能发生的干旱,或者由于地下水进入坑道而导致的水位下降等影响事件。理想情况下,坑道周边岩体的渗透性不应很强,从而保证流入坑道的水流强度适中; 同时坑道顶部区域岩体的渗透性要高得多,可确保地下水能充分补给。如果自然条件达不到要求,可通过在坑道上方建造由一个小廊道组成的“水帘”来补救,这些小廊道也可用于辐射探测。这样可以保持恒定的水压。监测系统包括一个测量地下水压力的测压仪网络。法国有 8 个这样的坑道,分布在 3 个不同地点。
2.3. 盐穴储存
地下埋藏着大量的盐矿(NaCl)。在法国,盐矿的面积约为 20,000 km2,厚度可达1 km,通过溶解作用可以形成大型地下洞穴(图4)。挖一口类似采油的井直到盐矿层,井周围以金属外壳包裹,将井与它穿过的土石隔开,顶部用水泥固定在地面上,然后将直径较小的第二根管子插入其中(如同饮料瓶中的吸管)。通过第二根管子将淡水注入盐矿层,水溶解盐,产生的卤水通过两个金属管之间的环形空间涌出。卤水必须排入大海,或供应给以氯化钠为原料的化工厂。

[图片来源:斯托伦吉](图4 STATION DE L’ESSUYAGE ET D’EXPLOITATION擦拭和操作台,INJECTION D’EAU DOUCE淡水注入,SOUTIRAGE SAUMURE盐水抽吸,INJECTION DE FQUL注射液,DOUCHE DE SEL GEMME岩盐淋浴,COUCHE DE SEL GEMME宝石岩层,PROFONDEUR EN MÈTRES以米为单位的深度,METRES米,DISTANCES EN MÈTRES以米为单位的距离)
根据需要和盐矿层的规模,所产生的空腔体积可以从几千到超过一百万立方米。几个世纪以来,这一工艺一直被用作生产盐水的采矿技术。从 20 世纪 50 年代(法
国从 1970 年)开始,以这种方式形成的洞穴被用来储存碳氢化合物。在同一个储存点有几十个洞穴。它可以储存液体、气体、液化或超临界形式的各种类型碳氢化合物及其他产品,如氢气、氦气或压缩空气。
储存液体或液化产品时,用于浸出的中心管留在洞穴中。储存的产品密度低于盐水,并在其上方“漂浮”。当盐水通过中心管注入时,产品通过环形空间萃取,反之亦然。因此,应在土壤表面设置盐水罐。溶洞中流体的压力,其顺序为γbz,其中γb=0.012 MPa/m是盐水的体积重量,其随时间变化很小。
储存天然气时,首先要将洞穴中的盐水排空。操作与气瓶相同:压力因存储大小而变化,PV=mrT;洞穴的(绝对)温度T和体积V变化不大,气体的压力P与储存的气体质量m近似成比例。但是,设置了极值。套管下端(管脚)的最大梯度通常为0.018 MPa/m,为防止压裂提供了裕度(参见工业水力压裂的挑战)。
最小压力通常是考虑到洞穴的稳定性而设定的。事实上,虽然盐是固体,但从长期来看,它就像一种极粘的流体(它会流动),并且空腔往往会闭合。当洞穴很深(1300米以上)且气压较低时,每年的闭合速度可达几个百分点,而且闭合过程也会导致地面下降。然而,由于盐洞直径/深度比很低,其下降幅度相对较小(几十厘米)。因此,在世界上大约2000个储藏库中,没有已知的与盐储藏库有关的陆地塌陷案例。法国大约有80个盐储库,分布在六个地点:德拉姆的泰尔桑尼和勒格兰德塞尔,艾因的埃特雷斯和维里亚,普罗旺斯-阿尔卑斯省的马诺斯克气体储气库和液体储气库。
3. 成本
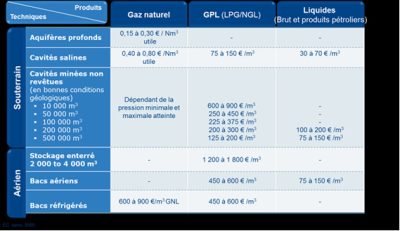
[图片来源:地质库](表1 Techniques技术,Produits产品,Gaz naturel天然气,GPL(LPG/NGL)液化石油气,Liquides(Brut et produits petroliers)液体(原油和石油产品),Aquifères profond
表 1 由法国Geostock公司提供,详细展示了不同地下储存成本的大小。一般来说,地下存储的成本远低于架空存储(即地面存储)的成本。以盐穴储气库为例,每立方米真空盐穴的价格为 30-70 欧元,对比石油价格,仅占其一小部分(每桶石油大约 160L,在 2017 年售价 50 美元,但在几年前售价 100 美元,相当于每立方米石油售价300-600 欧元)。开采洞穴的成本更高,但成本随着洞穴的增大而迅速降低。含水层储气库的造价一般为每“有效”立方米0.15-30 欧元,即按需注采时每立方米的成本,没有考虑储气库“垫层”的成本。
4. 风险
埃文斯的研究[2]表明,在石油产品生产、储存和分销的完整链中,地下储存是最不容易发生事故的环节。原因很简单[3]:在地底深处,空气中没有氧气,产品不会爆炸或燃烧;地下的储气受到数百米大地的保护,免受外部攻击、龙卷风、火灾、飞机失事、恶意袭击;而且它们对地震不是很敏感,地震的最大影响往往发生在地面上。同时,就地表占用面积而言,地下储存非常的经济实惠(封面图)。
以气态或液化烃为例,井口破裂可能导致完全排空。在欧洲,天然气井(洞穴或含水层)配备了一个地下安全阀,一旦井口发生故障,该阀会自动启动。
储库的金属套管或水泥套管是最常发生事故的位置,当其存在质量问题时,注采的能源就能在经过地面时接触到金属外壳从而引发事故,例如最近发生在加利福尼亚州阿利索峡谷的事故。在法国,天然气储存需要两根金属管,第二根金属管与水泥套管形成环形空间,底部封闭,并充满水。因此,一旦发生油气泄漏,就可在第二根金属管的表面检测到。
预防/监测还包括泄漏测试。在美国,泄漏测试在整个储存期内定期进行。对于盐穴,这些测试包括用难以与盐水(燃料油或氮气)混合的流体填充井中的环形空间,并在几天内通过测量流体表面的深度来检查其质量是否保持恒定。这项测试准确度高,在美国是强制性的。
5. 储存设施的废弃
经验表明,矿井废弃后会对矿井表面的土地稳定和地下水的恢复平衡造成不利影响。对于碳氢化合物储存,可利用已废弃的储库开展实验,比如奥尔恩河畔迈矿井的燃油储库和 Carresse 盐穴以及维克森和小库罗讷市白垩廊道的丙烷储库。
首要问题是清理储库壁上碳氢化合物的残留。这个过程中,必须小心关闭通道结构(井和钻孔)。对于废弃的含水层储库,分析遗留在其结构中垫层的长期特性是很有必要的。对于废弃的盐穴,通常将盐水灌入其中,检测留在底土上的大颗粒的动态变化。在该领域非常活跃的法国公司和学者的研究已经表明,当洞穴中盐水压力保持低于破碎压力时,可建立(两者)平衡(参见工业水力压裂的挑战)。
6、地下储库的未来
法国拥有完善的地下碳氢化合物储存设施,因此现有的技术可应用于其他能源产品和资源的储存。比如,可通过限制释放到大气中的温室气体数量或提高间歇性可再生电力(太阳能、风力涡轮机)后期生产的灵活性,为能源转型做出决定性贡献[4]这个问题并不总能得到充分解决。地下储库最常考虑的应用如下。
从大型生产商(水泥厂、钢铁工业)收集 CO2,并将其注入咸水层(以避免给饮用水资源造成负担)是 CO2 封存的手段之一。这种技术与含水层中的存储天然气有一定的相似性,因此,其技术体系可以参考含水层储存天然气的技术(几何识别、双套管、安全阀、历史匹配)并进一步发展。但是,两者也存在差异: CO2 可以以超临界状态储存——即以致密形式储存。它可以大量溶于水。此外,二氧化碳的限制期可能会比全球变暖高峰期更长,也许需要10个世纪的时间来确定。这就产生了在这段时间内进行监测的问题。最后需要说明,要注入的 CO2 质量远大于天然气储存中所含的 CO2 质量。例如,在挪威 Sleipner的三个主要的 CO2 注入点之一,注有 1650 万吨 CO2,超过了法国所有的天然气库中的 CO2(约 1000 万吨)。然而,就限制温室气体的大气排放而言,仅此站点的影响微乎其微。低廉的碳价阻碍了项目投资,但这种不利的环境可能会(随社会进步而)改变。
储氢(H2)。水电解产生的氢是储存间歇性能量周期性产生的多余电能的有效手段。氢气可注入天然气网络(高达10%);它可用于甲烷化或用作燃料。为实现碳氢化合物脱硫,得克萨斯州和大不列颠的盐穴中已经存储了大量的氢气,因此,大规模储存的手段将在需要时立即可用。
储存由二氧化碳产生的甲烷。甲烷化是指通过电解获得的氢气与甲烷燃烧后产生的二氧化碳结合形成甲烷(CH4)。它还可能涉及 O2 和 CO2 的储存。盐穴既提供了一个解决方案也带来了一些新问题,例如热力学问题,因为洞穴底部不可避免地留有少量盐水,而储存的二氧化碳可在其中大量溶解。
压缩空气储存。有两个盐穴,分别在德国和美国。在这两个盐穴中,过剩的电力会将夜间注入的空气压缩,然后在白天抽出,为涡轮机提供动力。由于气体被注入洞穴之前必须冷却,所以整体效率约为 50%。为了改善这一点,计划将压缩出口回收的热量储存(而不是储存在表面上)。然而,与每立方米天然气洞穴中储存的化学能相比,每立方米洞穴中储存的机械能意义不大。碳氢化合物的成功并非偶然!
这种存储形式会产生有趣的机械问题。比如在一个极大的储气洞穴中快速抽气,洞内水分扩张会使得气体快速冷却,尤其是当靠近绝热体时。在岩壁处,盐会收缩,并出现额外的拉伸应力,岩石对此耐受度较低:裂缝可能在冷却区域打开。这些效应已被广泛研究。似乎微裂缝区域仍然局限于洞穴壁上那一层薄薄的“皮肤”。
长期以来,法国一直有办法将其年天然气消耗量的 25%储存在地下。就液态烃而言,储存量约为年消耗的10%。依靠他们的技术,法国公司在世界各地运营和建造地下储存设施。能量转换是不可避免的,即使它的发展路径很难预测。新能源的存储需要巨大的储能空间,而油气储存过程中积累的技术知识对未来发展是一笔宝贵的财富。
参考资料及说明
封面照片:上普罗旺斯阿尔卑斯省马诺斯克附近盐洞中原油储存的地面设施[液态烃的储存;来源:土拨鼠图片库]
[1] Source: Key energy figures. Edition 2017. Ministry of Environment, Energy and the Sea in charge of international climate relations. Observation and Statistics Department. February 2017
[2] Evans, D.J. 2009. A review of underground fuel storage problems and putting risk into perspective with other areas of the energy supply chain. In Evans D. J. & Chadwick, R. A. (eds) Underground gas storage: worldwide experiences and future development in the UK and Europe. Geological Society of London Special Publication, 313, 173-216.
[3] Bérest P., Brouard B. 2003. Safety of salt caverns used for underground storage. Oil & Gas Science and Technology Journal – Rev. IFP, Vol. 58, 3:361-384.
[4] Ineris. Underground storage in the context of the energy transition. Ineris references, September 2016.
环境百科全书由环境和能源百科全书协会出版 (www.a3e.fr),该协会与格勒诺布尔阿尔卑斯大学和格勒诺布尔INP有合同关系,并由法国科学院赞助。
引用这篇文章: BEREST Pierre (2024年3月14日), 天然气和碳氢化合物的地下储存:能源转型的前景, 环境百科全书,咨询于 2025年4月11日 [在线ISSN 2555-0950]网址: https://www.encyclopedie-environnement.org/zh/sol-zh/underground-storage-gas-and-hydrocarbons-prospects-for-energy-transition/.
环境百科全书中的文章是根据知识共享BY-NC-SA许可条款提供的,该许可授权复制的条件是:引用来源,不作商业使用,共享相同的初始条件,并且在每次重复使用或分发时复制知识共享BY-NC-SA许可声明。